Navigating Inventory Discrepancy: Best Practices and Strategies
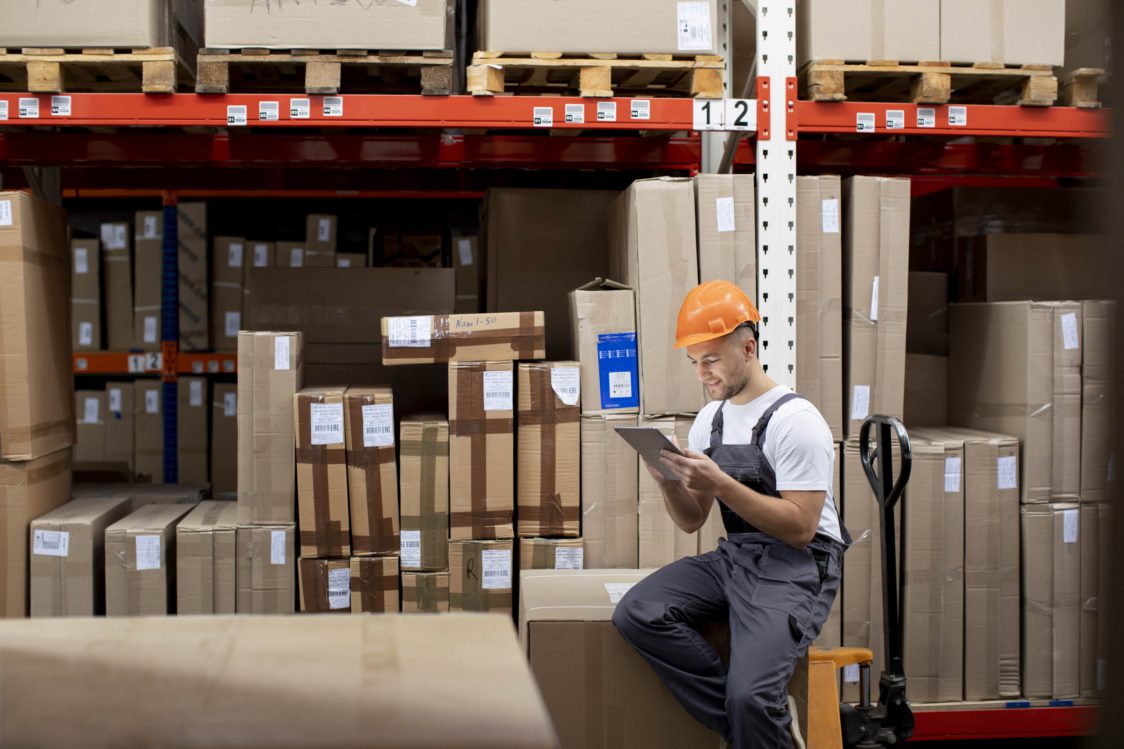
The disparity between the quantity that is listed in an organization’s inventory management system and the quantity that is actually physically accessible is known as inventory record inaccuracy (IRI) or inventory discrepancy. IRI may cause serious problems in the retail industry, such as stockouts and revenue losses brought on by needless restocking.
Inventory discrepancy has a detrimental impact on replenishment estimates and inventory availability. IRI may be expensive for a business since it may interfere with the efficiency of the whole supply chain. IRI can result in a revenue loss of more than 1% of sales and more than 3% of gross profit in a retail setting.
Causes of Inventory Discrepancy
Stock loss
- Stock loss sometimes referred to as shrinkage in the business, refers to all kinds of losses of the goods that are offered for sale.
- Theft is an illustration that comes up frequently. This crime may be performed by both customers (external theft) and workers (internal theft).
- Additionally, it covers employee and customer collusion as well as unauthorised stock usage (such as eating) by both consumers and workers. Additionally, when conducting replenishment chores for their own inventory, the vendors have the ability to steal goods from the shop.
- Stock loss can also happen when goods lose their marketability due to spoilage, damage, or expiration.
Transaction error
- Typically, transaction errors happen on the facility’s inbound and outgoing sides. Shipments from the suppliers must be registered in the store information system on the inbound side.
- The inventory record could not correctly reflect the real stock if there is a disparity between the shipping record and the actual shipment that goes unreported by the receiving clerk.
- The checkout registers are not immune from contributing to inventory discrepancy records on the outgoing side.
Inaccessible inventory
- Products that exist someplace in the facility but are not accessible because they cannot be located are referred to as inventory discrepancy. This may occur if a customer removes a product from the shelf and sets it somewhere else.
- The store’s rear room or any other storage space may likewise experience it. Eventually, the inaccessible goods will be located and prepared for sale.
- However, it can be some time before this occurs, and in the meanwhile, the unavailable items are effectively worthless in terms of sales.
Incorrect product identification
- The identification of a product incorrectly can happen in a number of ways. Both suppliers and retailers have the ability to apply incorrect labels on the goods.
- The inventory record for the incorrect products will be altered when the bar codes on these labels are scanned during receiving or checkout.
- Manual inventory counts might sometimes result in incorrect identification.
How to avoid Inventory Discrepancy
The danger of supply chain problems, such as inaccurate client orders, product shortages, theft, damages, and financial loss for your company, is reduced by inventory accuracy. Inventory discrepancy might occur if you’re in charge of keeping significant numbers of several SKUs. Not that there aren’t measures to lessen hazards, though. Here are the recommended practices for preventing significant inventory discrepancy.
Communication with suppliers
When it comes to improving inventory control, having good supplier connections may make all the difference. If your supplier provides updates on your pipeline inventory at each stage, you can better plan when to receive it, how much of each SKU you’re anticipating, and have it stored properly and promptly. Strong communication with your supplier helps prevent inventory discrepancy in the long term, as well as stockouts, overstocking, and lost goods.
Update your inventory management systems
Your business productivity is undoubtedly being held back by out-of-date technological solutions in this dramatically changing retail environment. With sophisticated inventory management software, you can be confident that SKU tracking is done automatically and that the inventory levels that are recorded are always current and correct.
Training employees
Your team has to have access to skill-building seminars on everything from digital inventory recording and effective stock counts to inventory planning, warehouse setup, and warehouse receiving. Utilise this as an opportunity to explain to them the immediate and indirect effects that inventory discrepancies have on them, such as how they influence promotions, salary, employee profit sharing, and more. There may be fewer human mistakes once people are aware of the best practices.
Partner with a 3PL
Errors, no matter how tiny, may have a big impact on logistical operations. Accuracy, efficiency, and faults not only reduce earnings, but also have a negative effect on the customer experience. A 3PL gives better control while reducing expenses and saving you time by managing and automating your inventory management process.
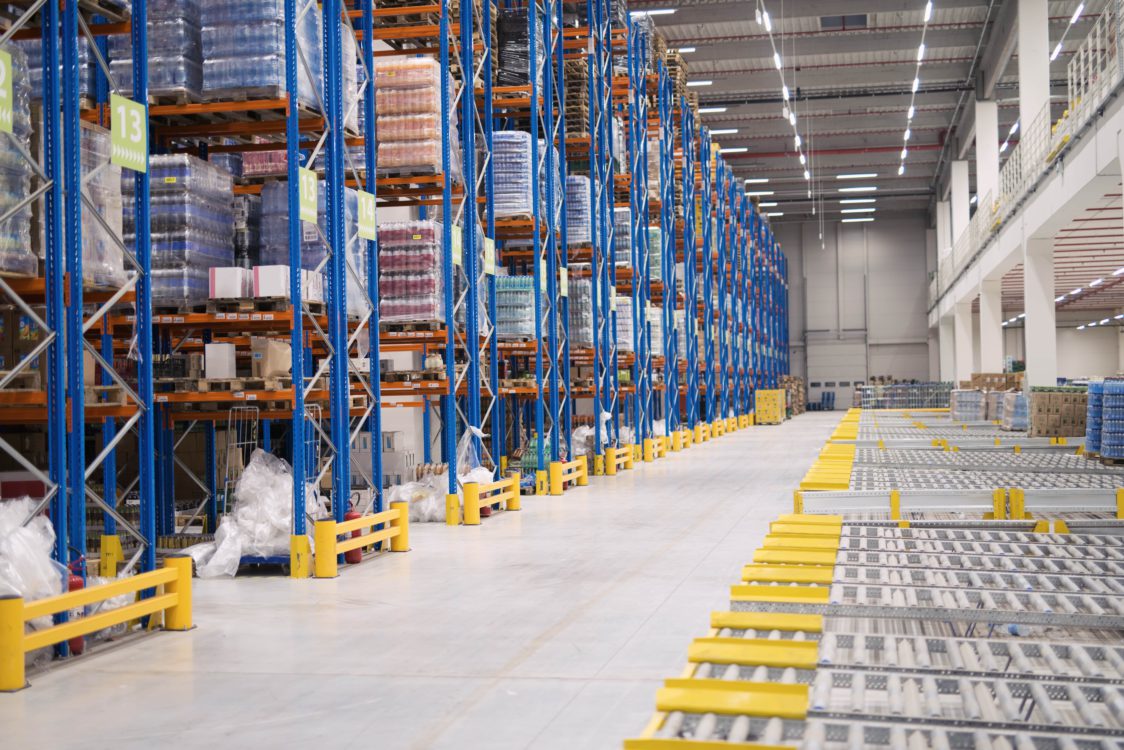
Approaches to Solution
No Information Scenario
In the No Information Scenario, the inventory manager orders stock in accordance with the routine, periodic inventory check without being aware that mistakes are made. The estimated cost in the No Information Scenario fluctuates over time as a result of mistakes that build up from one period to the next.
Informed Scenario
The management making the decisions, in this case, is aware that mistakes are occurring and is familiar with their distribution (expected value and standard deviation). In a system with faults, which most inventory systems unquestionably have, the best course of action is static. The basic inventory level fluctuates throughout time as a result of the random variable of demand and the components even if the base stock policy is the best one.
Static Informed Scenario
The sole difference between this and the Informed Scenario is that in this case, the inventory manager simply considers the expected value of mistakes rather than their distribution. He does this because it is necessary to adopt a static base stock policy (which is obviously simpler to implement) and since this is the only accessible information. The progression closely resembles that of the Informed Scenario.
The Full Information Scenario
Complete information allows misplacement mistakes to be instantly identified and prevents incorrect scanning errors. Even though some researchers in the field of contemporary information data-gathering systems assert that they have decreased shrinkage, we presume that shrinking still takes place. Even so, shrinking happens but is instantly apparent.
Implementing Robust Inventory Management Systems
A. Centralized Inventory Tracking System
Businesses should buy a centralized inventory tracking system in order to effectively manage their inventory discrepancy. This system constantly provides a comprehensive view of inventory by combining data from multiple sales channels, warehouses, and sales points into a single platform. Businesses can quickly find any issues and fix them with real-time inventory and movement updates.
Inventory management processes are simplified by the centralized inventory tracking system, which eliminates the need for manual entry of information and reduces human error rates. Also, it facilitates seamless integration with other business systems, such as accounting and CRM software, which leads to more efficient workflows.
B. Barcode and RFID Technology
Barcodes and RFID technology are essential tools for precise tracking and recording of inventory. Businesses can automate the data capture process by using barcodes and RFID tags on products and storage units. This results in faster and error-free stock counting and replenishment.
Barcode scanners and RFID readers make it easy for employees to scan items and update inventory records in real-time. It not only reduces the chance of data entry errors, but it also speeds up inventory processes, which means more efficient order fulfilment and shorter lead times.
Barcode and RFID technology also makes it easier to see and track inventory. Businesses have the ability to monitor the movement of goods throughout the supply chain, from the time they reach the warehouse to the time they are delivered to the consumers. Businesses can take proactive measures to ensure inventory accuracy by using this level of visibility, which helps spot potential issues.
Conclusion
The disparity between the quantity that is listed in an organization’s inventory management system and the quantity that is actually physically accessible is known as inventory record inaccuracy (IRI) or inventory discrepancy. Inventory discrepancy has a detrimental impact on replenishment estimates and inventory availability. Inventory discrepancy might occur if you’re in charge of keeping significant numbers of several SKUs. Not that there aren’t measures to lessen hazards, though. Here are the recommended practices for preventing significant inventory discrepancy. Businesses should buy a centralized inventory tracking system in order to effectively manage their inventory discrepancy.