All about the Average Cost Meaning in Logistics
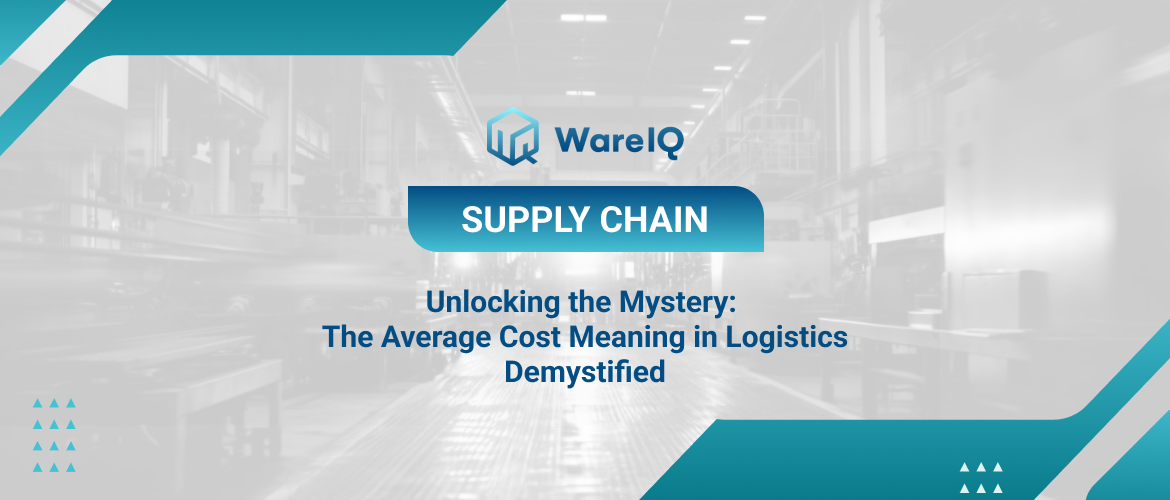
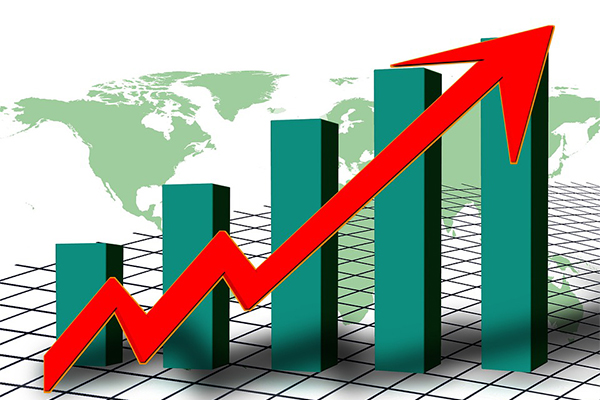
Logistics expenses comprise all costs connected with transporting items, including those spent during raw material sourcing, customer order fulfilment, and all processes in between. They are concerned about the expenses of transporting, transferring, and storing goods. However, inadequate decision-making preparation leads to high pricing.
A logistics cost is the entire amount of money spent by an organisation while moving a product. It would pay for the transportation of raw materials from the supplier. It stores them in a warehouse until they are ready for distribution. It also includes the cost of conveying finished items to the client.
- Types of Logistics Costs
- Difference between Logistics Types
- FAQs
- What are logistics Costs?
- How does inadequate decision-making affect logistics costs?
- What is the total amount of money spent by an organization while moving a product?
- What is the impact of rising warehouse costs on logistics expenses?
- Which component of logistics typically incurs the most significant expenses for a company?
- What are inbound logistics in terms of transportation costs?
- Why is last-mile delivery considered the most expensive part of the supply chain?
- How does labour contribute to variable logistics costs?
- What is the impact of excess inventory on cash flow?
- How does poor inventory management affect customer satisfaction?
Types of Logistics Costs
Inventory Management Costs
Whether you make your own items in-house or utilise a third-party manufacturer, you’ll need a location to keep your inventory. And the more merchandise you have, the more room you’ll require. Unfortunately, rising warehouse costs and restricted availability make it more difficult than ever to secure a leasing space.
Rental renewals in the United States climbed by an average of 25% this year, owing to a scarcity of accessible warehouse space caused by the expanding number of ecommerce enterprises. You could prevent this by purchasing your own warehouse space altogether, but it won’t be cheap.
Transportation and Logistics
Transportation and distribution are the most expensive logistics charges for any firm, whether you utilise third-party logistics service providers (3PL) like a reverse logistics company or an in-house team. Inbound logistics, such as carrying items from the manufacturer to your warehouse, are low-cost transportation jobs that entail consolidating big shipments in a single place. Outbound logistics, such as last-mile deliveries, are significantly more expensive.
Delivery
The term “last-mile delivery” refers to the act of delivering things straight to your clients. It is usually the last stage of distribution. Because carriers must make several trips to deliver tiny quantities of merchandise to consumers, these deliveries consume the greatest time and resources. Drivers may encounter security gates or reception desks, each with its own protocol for reception, which can further impede delivery. As a result, last-mile delivery is the most expensive part of your supply chain, accounting for half of the overall cost of shipping.
Labour
The personnel who manufacture, manage, and deliver your items is a variable logistics cost. However, the amount you’ll spend is determined by where your employees are located and the average wage in that area.
Difference between Logistics Types
Logistics Cost Types | Differences |
Cost of Inventory Management | Impact on cash flow: Excess inventory ties up capital. If there’s too much stock, cash that could be used elsewhere is consumed. If too little inventory is held, sales can be lost.Faulty forecasts: Inaccurate demand forecasts can lead to surplus or inadequate inventory levels.Shipping delays: Inefficient inventory management can result in delayed shipments and dissatisfied customers.Rising production costs: Poor inventory control can lead to higher production costs and reduced profitability.Unused or outdated stock: Failure to manage inventory properly may lead to obsolete or unused items that incur costs.Low inventory turnover rate: Low turnover rates mean items sit too long, tying up capital and increasing costs.Variable and erratic overhead expense: Inefficient inventory management can result in unpredictable overhead costs.Data entry mistakes (for tracking): Manual errors in tracking inventory can lead to mismanagement and costly issues.Lost clients: Inventory issues may lead to unsatisfied customers and lost sales. |
Cost of Warehousing | Performance data evaluation: Evaluating warehouse performance is critical for efficiency and cost control.Picking accuracy: Ensuring high accuracy in picking orders reduces errors and associated costs.Inventory shrinkage rate: Monitoring and managing shrinkage to minimize losses and expenses.Customer growth tracking: Tracking the growth of the customer base affects warehouse needs and costs. |
Cost of Switching Modes of Transportation | Associated with mode-shifting and fulfilment: Switching transportation modes may introduce complexities and costs.Impacted by online purchasing trends: E-commerce trends require efficient mode-shifting to meet customer expectations.Lack of visibility across transportation and distribution touchpoints: Poor visibility increases indirect costs.Added pressure on supply chain transportation links: Inefficient inventory management stresses transportation links, resulting in additional costs. |
Costs of Distribution | Influenced by throughput times: Efficient throughput times impact distribution costs positively.Scheduling: Timely scheduling reduces wait times and associated expenses.Vehicle use: Optimal vehicle use minimizes transportation costs and improves efficiency.Vendor efficiency: Efficient vendor collaboration affects distribution costs.Greater variability in supply chain optimization: Greater variability increases tracking and data management challenges. |
Cost of Customer Service | Vital for customer satisfaction: High-quality customer service is essential for customer retention.Impacts customer retention: Poor customer service can lead to customer churn and increased acquisition costs.Includes resolving problems efficiently: Efficient problem resolution minimizes the cost of addressing customer issues.Investing in excellent customer service: Allocating resources to customer service affects overall expenses and customer satisfaction. |
FAQs
What are logistics Costs?
Logistics Costs encompass all costs related to transporting goods, including raw material sourcing and customer order fulfilment.
How does inadequate decision-making affect logistics costs?
Poor decision-making can lead to higher logistics costs due to inefficient planning and resource allocation.
What is the total amount of money spent by an organization while moving a product?
This is referred to as a logistics cost, covering transportation, storage, and distribution expenses.
What is the impact of rising warehouse costs on logistics expenses?
Rising warehouse costs, along with limited availability, can significantly increase logistics expenses for storing inventory.
Which component of logistics typically incurs the most significant expenses for a company?
Transportation and distribution are the most expensive components of logistics costs for most companies.
What are inbound logistics in terms of transportation costs?
Inbound logistics involve the transportation of goods from the manufacturer to the company’s warehouse, usually at a lower cost.
Why is last-mile delivery considered the most expensive part of the supply chain?
Last-mile delivery is the costliest because it involves multiple trips to deliver small quantities of goods to consumers, often facing various obstacles and delays.
How does labour contribute to variable logistics costs?
Labour costs vary based on employee location and local wage rates, impacting overall logistics costs.
What is the impact of excess inventory on cash flow?
Excess inventory ties up capital, reducing cash flow available for other purposes.
How does poor inventory management affect customer satisfaction?
Inefficient inventory management can lead to shipping delays, unsatisfied customers, and potential loss of sales, affecting customer satisfaction.