How to Fix Inventory Mismatch in Warehouses Caused by Courier Returns Reconciliation
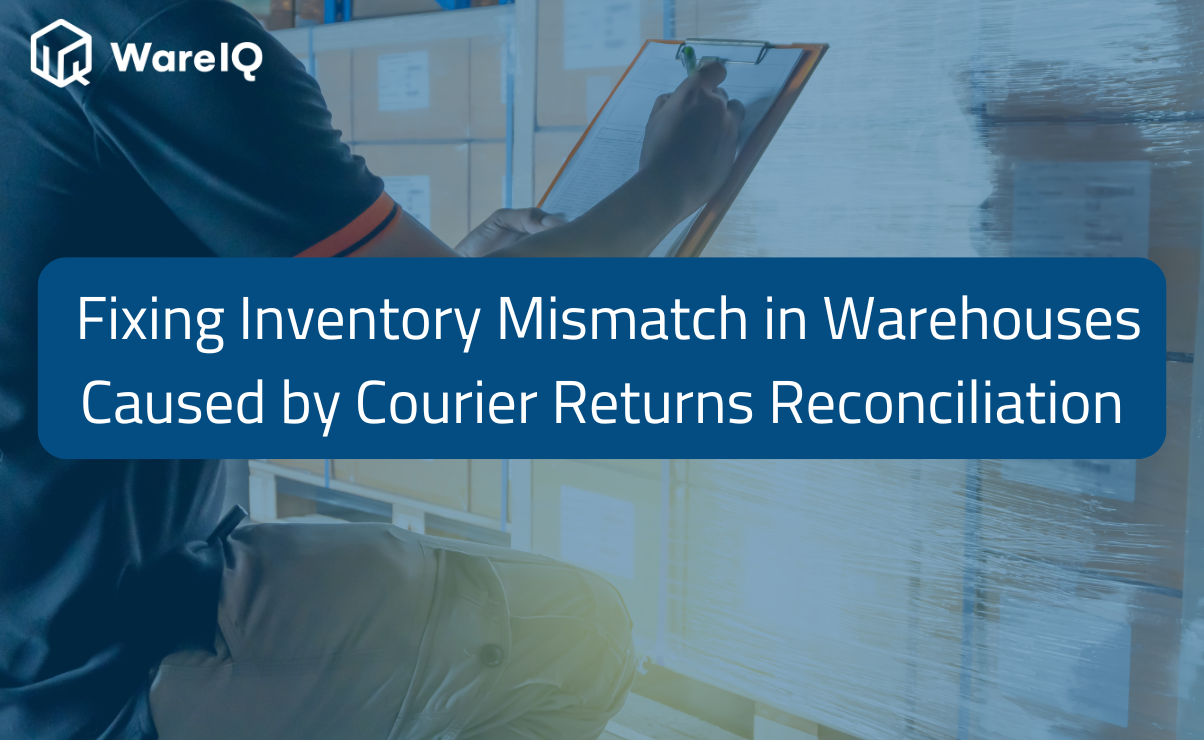
Inventory mismatch is a significant issue for eCommerce businesses, especially when discrepancies arise between couriers’ reports and warehouse records. This is particularly challenging when reconciling returns (RTO – Return to Origin, and DTO – Delivered to Origin), which can disrupt inventory accuracy, lead to lost sales opportunities, and diminish customer satisfaction.
In this article, we’ll explore solutions for resolving inventory mismatch in warehouses caused by courier returns.
At WareIQ, we’ve developed robust processes and technologies to tackle this problem head-on, ensuring seamless courier returns reconciliation and accurate warehouse management.
The Problem: Inventory Mismatch Due to Courier Returns
When returns are processed, several steps need to be executed precisely:
- The courier picks up the return from the customer.
- The returned goods are delivered to the fulfillment center or warehouse.
- The warehouse logs the receipt and updates the inventory system.
However, mismatches often occur when:
- Courier Errors: Couriers mark returns as delivered, but the warehouse doesn’t receive or log them properly.
- Warehouse Log Issues: The warehouse may receive returns but fail to update the inventory records accurately.
- System Integration Gaps: Poor synchronization between the courier and warehouse systems leads to data discrepancies.
Without proper handling, these discrepancies cause inventory mismatches, affecting stock accuracy, fulfillment speed, and customer service.
How WareIQ Solves Inventory mismatch due to Courier Returns Reconciliation
At WareIQ, we utilize a combination of technology, best practices, and continuous monitoring to prevent and resolve inventory mismatches caused by courier returns.
1. Real-Time Data Synchronization with Couriers
WareIQ ensures real-time syncing of data between couriers and warehouses through:
- API Integrations: Our system is integrated with various courier services, allowing automated status updates for returned goods. When a courier picks up a return, it’s tracked in real-time until the package arrives at the warehouse.
- Automated Tracking: Both couriers and warehouses use barcode/QR code technology to scan returns at multiple checkpoints, ensuring accurate logging of every return.
For more on how WareIQ optimizes inventory processes, read The Ultimate Guide to Streamlining Physical Inventory Processes in Warehouses.
2. Unique Return ID System
To prevent miscommunication between couriers and warehouses, WareIQ implements a unique return ID system:
- Every return is assigned a unique barcode or QR code that connects it to a specific order.
- Both the courier and warehouse scan the return ID during the pickup and receipt stages, ensuring that the process is trackable and error-free.
3. Automated Reconciliation of Returns
WareIQ reduces manual efforts in reconciling returns by automating key steps:
- Automated Data Matching: Our system automatically cross-checks the courier’s records of delivered returns with what the warehouse has logged. This drastically reduces the chance of human error.
- Real-Time Discrepancy Alerts: If there’s a mismatch between the courier’s claimed returns and the warehouse’s records, our system instantly flags the issue. This allows our operations team to resolve discrepancies swiftly before they impact inventory levels.
You can explore more of our inventory best practices in our blog on WareIQ Standard Operating Procedure for Inventory Management Excellence.
4. Improved Courier-Warehouse Communication
WareIQ fosters strong relationships between couriers and warehouses by standardizing communication:
- Shared Data Logs: WareIQ ensures that couriers and warehouse teams share detailed data about returns in real-time. This includes timestamps, item descriptions, and receipt confirmations.
- Escalation Procedures: When there’s a discrepancy (e.g., the courier marks a return as delivered, but the warehouse hasn’t logged it), we have a clear escalation procedure to resolve the issue quickly, ensuring no delays or disruptions in inventory accuracy.
5. Regular Cycle Counts and Audits
To ensure ongoing accuracy, WareIQ performs regular cycle counts and audits of warehouse inventory. This helps us identify and correct any discrepancies before they become bigger problems.
- Cycle Counting: This process involves counting portions of inventory on a regular basis instead of relying on annual counts, ensuring our stock levels are accurate at all times. When discrepancies are flagged, we promptly investigate and correct the mismatch.
Learn more about the benefits of cycle counting in our post on Cycle Inventory Management: Riding the Waves of Efficiency.
Benefits of WareIQ’s Approach to Courier Returns Reconciliation
By leveraging technology and rigorous processes, WareIQ provides several key benefits to eCommerce businesses:
- Increased Inventory Accuracy: Our automated systems ensure real-time updates of returns, reducing inventory mismatches.
- Faster Issue Resolution: Real-time discrepancy alerts and escalation processes ensure that courier return issues are identified and resolved quickly.
- Operational Efficiency: By automating return tracking and reconciliation, we minimize the need for manual intervention, reducing human error.
- Improved Transparency: With real-time data syncing and shared logs between couriers and warehouses, all stakeholders have visibility into the return process.
Conclusion
Inventory mismatches caused by courier returns reconciliation can be a headache for eCommerce businesses, but with WareIQ’s technology and processes, you can rest assured that your inventory will remain accurate and your returns will be handled smoothly. By automating reconciliation, improving communication, and performing regular audits, WareIQ ensures your warehouse operations are always optimized for efficiency and accuracy.
For more insights into optimizing your inventory management, check out our other related blogs: