Stock Discrepancy: Definition, 5 Main Causes and Top 7 Methods to Avoid Inventory Discrepancy in 2025 in eCommerce

The fast-evolving business trends and technologies bring new challenges to every organization. To mitigate the issues of the end-to-end supply chain and cope with customer expectations, organizations are constantly focusing on reducing the delivery lead time. And one of the essential steps to reduce the lead time is to manage inventories in every form like raw material, semi-finished products, and final products.
Experts define inventory as a necessary evil. It is essential to run the business, but it blocks the business capital in the form of materials. Therefore, it is essential to manage accurate inventory. The stock discrepancy is one of the major challenges in inventory management, especially in the eCommerce business.
This article will take you through a brief definition of a stock discrepancy, its primary reasons, and the best practices to avoid inventory discrepancy.
What is Stock Discrepancy?
Stock discrepancy refers to the variety of physical available stock or inventory of items with respect to the current inventory in records or systems. To run a successful business of any size, maintaining accurate stock is vital. But inventory variation is a common scenario in a practical situation. In the case of industries like e-commerce, where you need to deal with a massive number of different SKUs, quick and error-free product transfer, and handling hundreds of last-mile deliveries, the chances of inventory mismatch increases.
Minor inventory discrepancies can be managed easily, but major inventory discrepancies can lead to considerable losses to your organization. Therefore, you must have a robust system to check inventories, find loopholes and implement best practices to avoid any untoward situations.
WareIQ, an eCommerce fulfillment company, empowers online brands with a superior-tech platform to compete with Amazon like service levels by bringing their average delivery timelines from 5-10 days to 1-2 days.
5 Main Causes of Inventory Discrepancy
Managing inventory throughout an eCommerce supply chain may sound easy, but it is a complicated task. You need to deal with thousands and lakhs of inward receipts and outward delivery day in and day out. Tracking every material movement, delivering the right product to the right place at the right quantity, and above all, managing inventory accuracy is nothing short of a nightmare.
But the task becomes easy if you know the probable causes of inventory discrepancy and how to avoid them. Here are some major causes of Inventory Discrepancy.
Inventory shrinkage
As the name suggests, when there is a shortage in the actual inventory compared to the stock in the records, it is known as inventory shrinkage. Simply put, it refers to when the physical stock of any item is less than the system stock. There are some probable reasons behind such discrepancies:
- Pilferage or Theft: Here are two possibilities:
- If a person involved in operations may pilferage items. Or,
- Some outsiders may steal.
- Administrative errors: There may be a chance of error in the accounting system, which eventually decreases the item’s quantity.
- Vendor Fraud: Manufacturers/suppliers may have sent you fewer number items than they billed for it.
Misplaced inventory
There is a place for every material in modern warehouses, and it is described in the inventory management system. Whenever the warehouse team receives an item, it is labelled first and then goes to its exact location. The same activity happens in the case of goods for delivery. In most industries, this activity is done by humans whereas, in some advanced warehouses, automated robots perform the task.
Discrepancies in inventory are primarily due to human errors like wrong material receipt or issuance, putting materials in wrong locations or incorrect labeling. Many times, suppliers also send the wrong materials unintentionally. Any of these mistakes can lead to a stock disrepancy.
Human error
One of the major causes of inventory discrepancy is human error. Apart from using highly advanced e-commerce warehouse management systems, some of the eCommerce end-to-end supply chain is driven by humans. And if your employees are not appropriately trained on how to receive, store, track and manage stocks, inventory discrepancy is unavoidable.
An inventory management system can assist people in managing the inventory efficiently, but they are the people who run the system. Firstly, to avoid human errors, you need to make sure that people understand the consequences of inventory variations. Keeping a standard operating procedure in place, displaying visual instructions, regular training, and frequent inventory audits are some of the best practices to avoid such errors.
Mismanaged returns
Return management does not add value to the business directly, but it has an impact on the balance sheet and revenue of the organization. Reverse logistics is as important as last-mile delivery. Poor return management can generate significant stock discrepancies and damages.
As there are several ways to treat the returned materials (restocked, refurbished, bad-quality-disposed, or scrapped), it is important to perform every activity carefully. If a bad-quality material is not stored back in the warehouse, it will create a stock discrepancy. Similarly, if a returned material is coded wrongly and placed in the location, it will show the wrong information in the system.
Effective return management not only helps you to avoid inventory discrepancies but also helps you to improve revenue.
Glitches in Inventory Management Software
Inventory management software must connect with the existing softwares/platforms businesses use in order to scale to accommodate advanced logistics. Choosing from hundreds of inventory management software solutions and understanding a slew of its features that necessitate training and continuous assistance is a difficult task. Choosing a wrong inventory management software can give further rise to stock discrepancy due to incorrect inventory counting, inventory forecasting etc.
7 Methods to Avoid Stock Discrepancy
Having a healthy inventory with accuracy is the key to delivering products on time. On the one hand, it improves customer satisfaction, and on the other, you can book more orders due to better visibility of your inventory status. Stock accuracy is beneficial in mitigating supply chain risks by avoiding incorrect customer orders, material shortages, theft, and damages.
Here are some best practices which can help you to avoid stock discrepancy.
Double Check During Counting of Stock
Physical inventory counting is a common process to identify and avoid inventory discrepancies. In this process, every item is checked physically, and then the stock is matched with the inventory records. Double counting can minimize errors. In case of a large inventory pool, you can use the ABC analysis method to identify high-value items and perform a double check on those items especially.
You can decide the frequency of physical counting on the basis of ABC and FMR strategy, and decide on a quarterly or annually sales velocity audit (for fast-moving items and slow-moving items).
Identify the Location of Stock
In a running eCommerce or production environment, the pace of materials movement is very fast, and there is a tendency to keep the same items in different locations. It is also important to check whether similar items are mixed with each other or not. With a slight change in design, the item code changes, but identifying the difference between such items becomes challenging. While performing physical inventory counting, you must check all the locations thoroughly and avoid the mixing of similar materials.
Check the levels of Inwards & Outwards Stock
To improve the inventory accuracy of your warehouse, you must ensure a strict inward and outward process. During the inwards process, checking every item along with their vendor invoices can help avoid major inventory mismatches. Often suppliers inadvertently send similar items with different item codes, leading to stock variation.
Communicate with Manufacturers
Suppliers play a significant role in an efficient inventory management process. You should establish strong communication with your vendors so that any issues, especially inventory variations, can be communicated immediately. If you inform your supplier about any stock discrepancies during the inward process, they can also check at their end and resolve the problem at the moment. Moreover, training the supplier’s staff can also make a big difference and help run your business smoothly.
Strong and transparent communication with your vendors not only helps you to manage inventory discrepancies but also helps avoid a stock-out situation or overstocking and reduces the cost of poor quality (COPQ).
Opt for an Inventory Management System
In this dynamic eCommerce environment, it is inevitable to have a smart inventory management system in place. It can help you to manage the stock levels, indicate the possible errors, and even help you to locate the item quickly. The advanced inventory management software is beneficial in significantly reducing the inventory counting time, which is a huge saving for any eCommerce business.
Train Employees
To make a big change, it is essential to increase awareness. As the technology in every field changes, new tools and techniques get introduced into the market every day. Adopting new technologies and training people on the fundamentals is essential. Employees need to know the correct method of inventory counting and its benefits and drawbacks for efficient inventory management.
Partner with a 3PL
Another best practice to avoid inventory variations is partnering with a 3PL like WareIQ. Being an experienced organization, WareIQ knows every nitty-gritty of inventory management and how to prevent stock discrepancies effectively. It offers stringent control and saves your time and money. Through the latest digitized tools, the overall inventory forecasting process is performed quickly and with high levels of transparency.
Conclusion
Technological advancement has increased buyers’ expectations in terms of competitive price, better material quality, and quick delivery. Poor inventory management with many discrepancies can hamper your revenue and result in customer dissatisfaction.
Human errors and inefficient systems are the root cause of a stock discrepancy. By implementing best practices, you can eliminate all bottlenecks and establish a healthy inventory system in your organization. Adopting intelligent inventory management software and partnering with an efficient 3PL like WareIQ can help manage your inventory better.
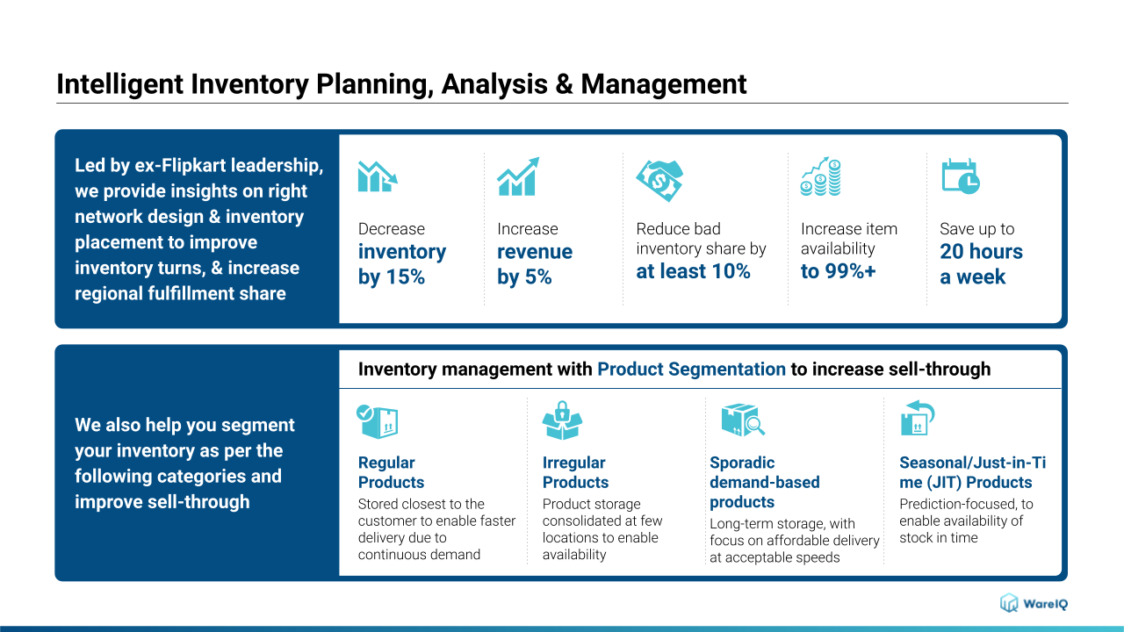
We at WareIQ give you full transparency of your inventory with real-time tracking features that make you monitor your product levels & status across our multiple warehouses from anywhere. As we know, return and reverse logistic is the major cause of the stock discrepancy, we provide RTO and logistics insurance to save your time, money, and other resources. If you keep the listed items on your website in our fulfillment centers, then you do not have to worry about inventory management and stock discrepancy. We are solely responsible for any discrepancy. If in case, it comes from your vendor’s side, you will be informed immediately.
- Pan India Fulfillment & Darkstore Network: Plug-and-play fulfillment infrastructure with no minimums, which is compliant with Amazon Seller Flex, Flipkart Assured, Myntra and other marketplaces
- Inventory & Network Planning Excellence: Best-in-class AI models for sales forecasting, product segmentation, and inventory management to reduce inventory by 40% and increase revenue by 10%.
- Vertically Integrated Fulfillment Tech Stack: Our Fulfillment Tech Solution supports integrations with 20+ top marketplaces & D2C platforms, and prominent national, regional and hyperlocal couriers, enhancing reach by covering deliveries for 27,000+ pin codes
- Supply Chain Productivity Applications: Integrate a host of supply chain productivity apps with a single-click to your existing CRMs, ERPs & accounting software to manage your logistics workflows from one command center. Use Apps like RTO Shield to get 100% RTO protection, Branded Tracking to turn your order tracking page into a profitable marketing channel, and many more.
Trusted by 300+ top Indian brands, we are helping them accelerate online sales and expedite their growth through a synergistic combination of advanced technology, robust fulfillment infrastructure & seller enablement services!WareIQ is backed by leading global investors including Y Combinator, Funders Club, Flexport, Pioneer Fund, Soma Capital, and Emles Venture Partner.