Inventory Audit & Reconciliation
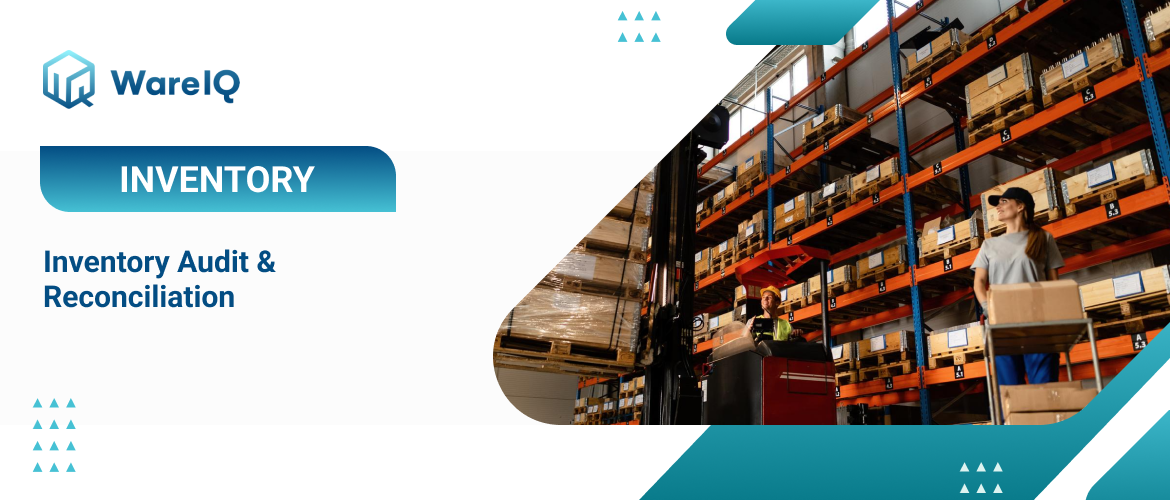
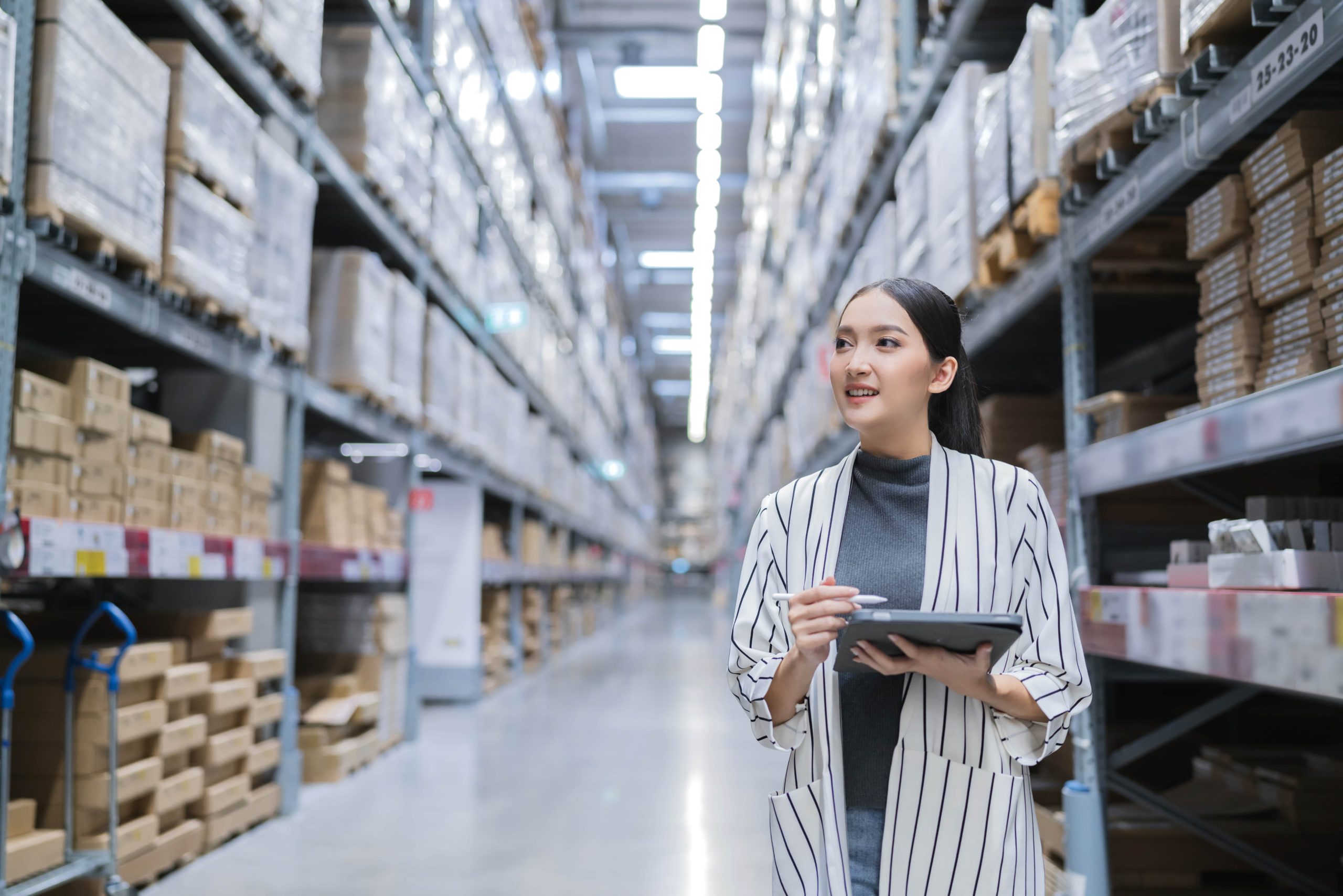
Inventory audit and Reconciliation of your inventory involves taking stock of what you have and ensuring that your stock records correspond to reality. To identify any inconsistencies that require attention, it’s crucial to reconcile your inventory on a regular basis. You must make a stock reconciliation report that accurately reflects your current inventory as well as the addition or deletion of stock items from the database in order to do this.
Inventory reconciliation involves comparing the stock’s physical count to the data listed in the inventory records. The first stage in reconciling your inventory is to count the actual stock that is retained for sale in comparison to the proof of stock that has previously been recorded. In order to rectify inventory errors, inventory reconciliation often entails counting damaged or outdated products and determining their origin. This strategy enhances inventory tracking systems and theft avoidance. The record should always represent the real stock, therefore when discrepancies are found, they should be resolved and updated accordingly.
Importance of Inventory Reconciliation
If inventory data and records for inventory on hand do not match, merchants have difficulties. Shrinkage is unavoidable, even with the greatest inventory management tools. Compared to what is recorded, there may be an excess or a lack of products in stock.
By routinely counting and reconciling inventory, retailers are better able to control loss and identify the root of discrepancies. It could be the outcome of administrative, human errors like wrong inventory counts or misplacing items in the stockroom, or it might be the outcome of a bigger problem like employee theft or supplier fraud.
How to carry out inventory reconciliation?
1. Count the Products
Count the available items and contrast the physical inventory with the inventory records. To cut down on mistakes, most businesses perform several counts. To match up with the records, this involves recording stock numbers and serial numbers. Your physical inventory can be done in a variety of ways. These are the typical approaches: cycle counting or a comprehensive inventory.
- Your team or a third-party inventory business will enter your facilities and count every physical item using the full inventory count technique. With a pencil and paper, barcode scanners, or RFID technologies, they can keep track of these counts.
- You’ll discover that counts are less difficult and demanding to do if you conduct cycle counts for your inventory monitoring purposes. In cycle counts, your staff members count particular goods or regions of your inventory every day. You’ll eventually count every item in your inventory, but only in parts.
- The benefit of this is that cycle counts may be performed without interfering with how your organisation runs on a daily basis. Because they just encompass a fraction of your warehouse, the smaller counts are less stressful and have a lower likelihood of inaccuracy.
2. Check Your Records
Ensure the accuracy of your inventory data, including the inventory control systems. This also entails precise and recent sales and invoicing. Compare the stock records for each item with the inventory records. Verify the accuracy of any stock numbers and serial numbers. Items without corresponding serial numbers or stock numbers should have their inventory-on-hand counts and supplier invoices reviewed. Similar to the counting procedure, most businesses double-check record matching to ensure correctness.
- Missing documentation is one of the most frequent reasons for inventory inconsistencies throughout the reconciliation process. Documentation pertaining to inventory should be filed and preserved in one easily accessible area. This procedure can be managed more easily with inventory management software.
- This one pretty much speaks for itself. There are occasions when merchandise enters your warehouse without being properly checked in. If you discover any unlisted objects during your count, it’s crucial to investigate them (by locating any relevant documentation, if feasible), add them to your inventory, and then list them for future counts.
3. Examine Discrepancies
You may probably find inconsistencies if you compare the outcomes of your inventory audit. After the inventory audit is finished, it’s time to deal with these errors. Math or human mistakes may be to blame for certain disparities. If it seems that’s not the case, the next step is to review sales data to look for any indication that sales may not have been correctly recorded. If you cannot locate any missing sales receipts, you could have lost or misplaced goods or evidence of fraud or crime.
4. Chase Down the Discrepancies
The appropriate degree of shrinkage in your firm is up to you to decide. It could be more time-consuming and expensive to identify the reason for the loss rather than continuing if there are a few items missing or they are of low worth. If you do decide to find it, start by looking at your systems, then your staff.
On the store floor, in the warehouse, or on eCommerce platforms, steps are frequently skipped throughout the recording process. To find out whether there is a reason for the disparity that can be resolved, it is important to interview the personnel who are in charge of each phase.
The crucial question in this situation is whether the disparity is significant enough to justify a resolution. You will occasionally need to “pick your battles” when it comes to resolving differences. For instance, it might not be worthwhile to invest time and effort in low-value things.
5. Compare results to previous reconciliations
Compare your inventory reconciliation results to earlier ones. This can help in the identification of areas that need more research as well as the detection of trends and patterns. This is particularly advantageous if there are any unresolved difficulties. Knowing about these irrational worries enables you to concentrate more carefully on those particular topics, either preventing future issues or helping you identify the issue’s root cause (shrink, human mistake, etc.).
6. Conduct reconciliation regularly
The advantages are lost if inventory reconciliation isn’t done on a regular basis. The regular maintenance of a stock reconciliation plan will increase data accuracy and save inventory costs. As a business grows, increasing inventory should be a key priority. By taking the effort to reconcile inventory, management is informed of any data inconsistencies and established stock processes are given a quality check. Using this information, managers may choose which inventory control systems to put in place to promote functionality and expansion. The amount of money spent on addressing stock mismanagement is reduced by establishing an efficient stock control system.
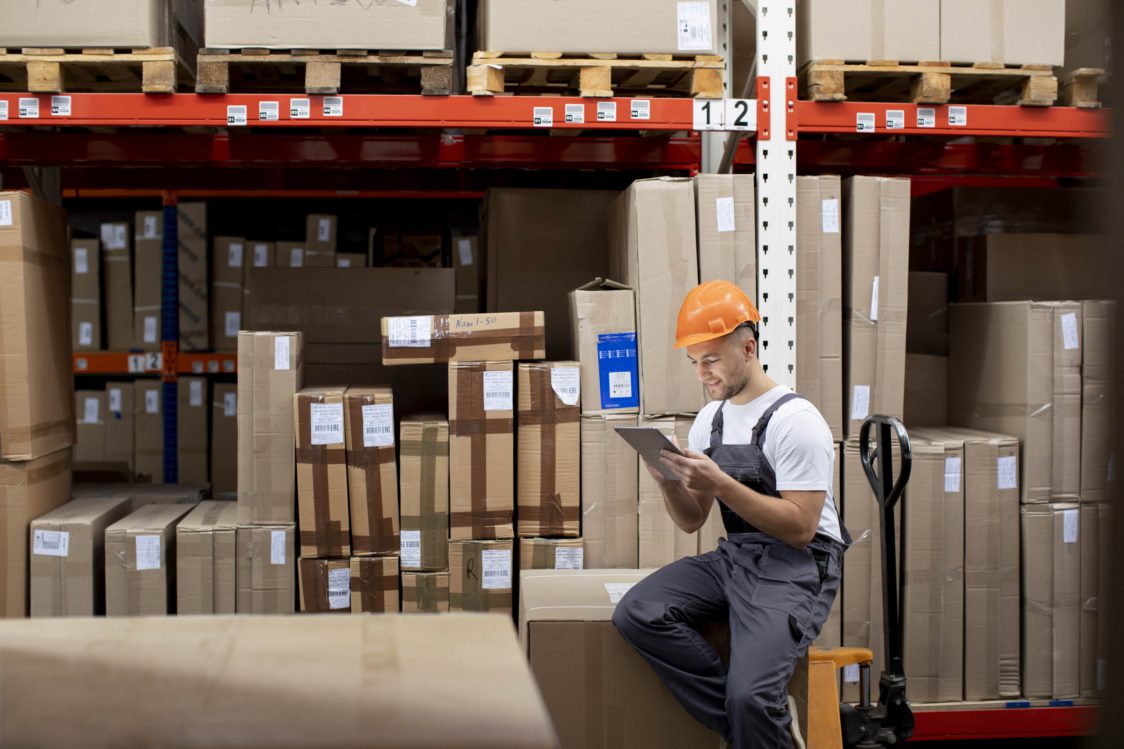
Inventory Audit Standards
Of course, a thorough inventory audit involves more than just stock counts. There are also monetary repercussions, such as avoiding potential tax issues by keeping your company in good standing with the number-crunching authorities. Additionally, each business will have its own set of warehouse guidelines to standardise internal processes and the administration of inventory audits.
1.The IRS
Businesses can select from a number of suitable methods for cost flow assumptions, including FIFO (First-In, First-Out), LIFO (Last-In, First-Out), and weighted average, according to the IRS. These presumptions affect financial statements and tax computations as well as how inventory costs are allocated. Businesses must choose and continuously use an acceptable cost flow assumption.
2. The SEC
All publicly listed US corporations must follow the financial reporting criteria set by the SEC. Both Generally Accepted Accounting Principles (GAAP) and International Financial Reporting Standards (IFRS) standards, which provide guidelines for inventory valuation, measurement, disclosure, and overall presentation of financial statements, must be followed by businesses in order to comply with SEC inventory audit rules.
3.The IFRS and AISB
These two regulating organisations are intertwined. Imagine the yin and yang of financial reporting on a global scale. International Financial Reporting Standards are established by the IASB, an independent body. In order to provide accurate financial reporting across international boundaries, compliance makes sure that companies adhere to globally recognised accounting norms for inventory ownership.
How WareIQ can Help in Inventory Audit?
- As a Record System, WareIQ provides Smart Inventory Audit Capabilities and a Smart Fulfillment Platform. It works well with top sales channels, WMS and ERP platforms, and courier partners.
- It lets you see records, purchase orders, credit notes, orders, and sales data in real-time. WareIQ reduces mistakes by ensuring error-free processes and real-time updates on WMS and fulfilment platforms through its scan-based warding, picking, and putaway operations.
- Furthermore, scan-based cycle counts on handheld devices increase counting accuracy, which allows for real-time execution without interfering with daily tasks. WareIQ’s smart features enable businesses to manage their inventory efficiently and guarantee more efficient and smooth operations.
- In a 90-day cycle timeline, WareIQ can help with its Daily Inventory Cycle Count with zero downtime. Our daily cycle counting process covers the entire inventory in a quarter, with 3.33% covered daily. It eliminates the need to stop operations for 5-7 days to count, which prevents business losses.
- By accounting for returned items, we guarantee no discrepancies. Return re-inventorization data is automatically synced and reflected within 24 hours, and real-time updates of Return QC rejects in the inventory master prevent discrepancies in the future.
- Our organized inventory storage system makes system updates simple. For easy later identification, all inventory items are marked and updated on our technology platform. Before picking, ensure that all inventory items are placed in the right bin, pallet, or rack.
- WareIQ’s efficient inventory management system allows businesses to maintain accurate inventory records, carry out daily cycle counts without delays, and ensure a smooth, organized storage process for simple operations.
Related read: Stock Audit: Objectives, Importance and 10 Procedures for Inventory Audit in eCommerce for 2025
Suggested read: Inside WareIQ’s Inventory Audit Strategy
Conclusion
Reconciling your inventory involves taking stock of what you have and ensuring that your stock records correspond to reality. You may probably find inconsistencies if you compare the outcomes of your inventory audit. After the inventory audit is finished, it’s time to deal with these errors. Math or human mistakes may be to blame for certain disparities. Additionally, each business will have its own set of warehouse guidelines to standardise internal processes and the administration of inventory audits.