Warehouse Material Handling: Best Practices
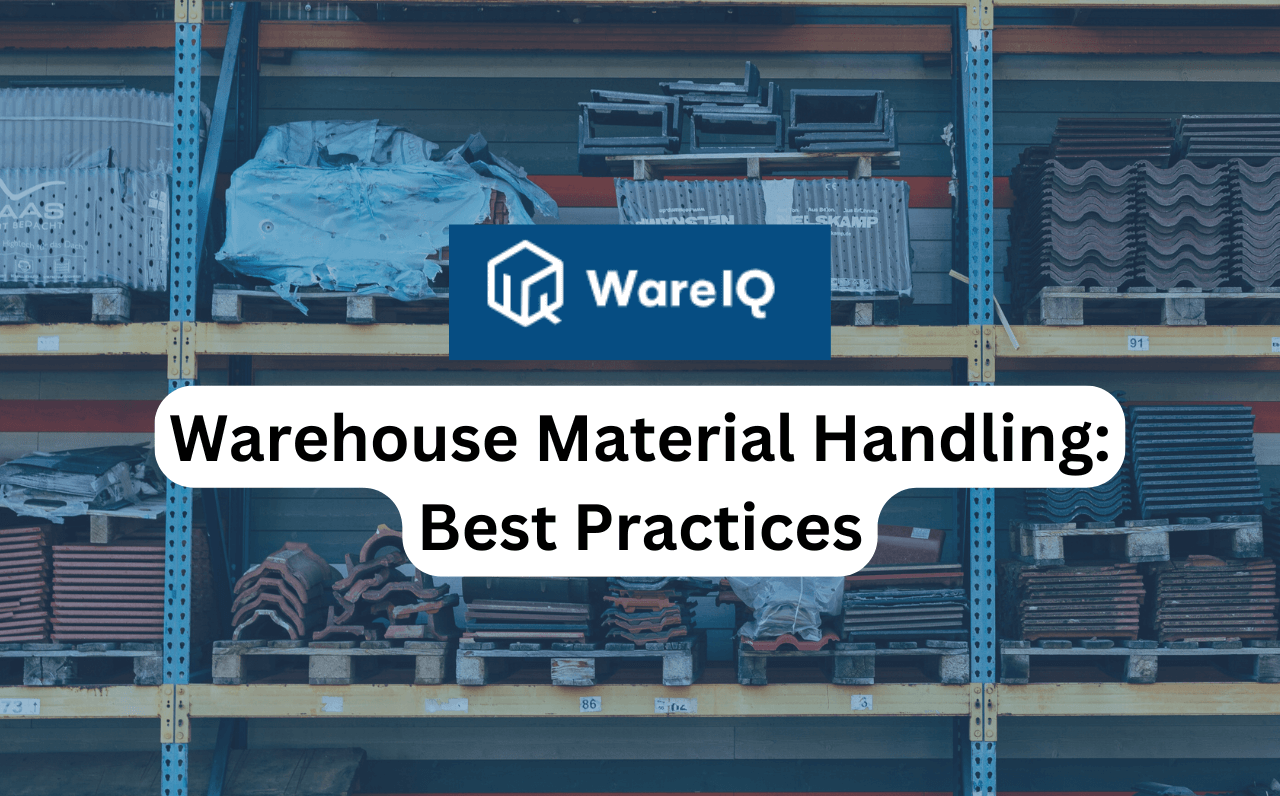
Warehouse material handling is the backbone of efficient logistics and supply chain management. It encompasses the movement, protection, storage, and control of materials within a warehouse. Effective material handling ensures that products are in the right place at the right time, enhancing productivity and reducing operational costs.
Notably, the U.S. warehousing industry employed approximately 445,780 labourers and freight, stock, and material movers in 2023, highlighting the sector’s significance. (bls.gov)
In this informative guide, we will explore some of the best practices for warehouse material handling. So, let’s get started!
Understanding Material Handling
What is Material Handling?
Material handling refers to the systematic movement of goods and materials throughout the manufacturing, warehousing, distribution, consumption, and disposal stages. It involves various operations such as lifting, transporting, storing, and protecting products. The primary goal is to ensure that materials are handled safely, efficiently, and cost-effectively.
Importance of Material Handling
Efficient material handling is crucial for several reasons:
- Safety: Proper handling reduces the risk of workplace injuries. For instance, as many as 20,000 workers are injured in forklift accidents each year. (kokeinc.com)
- Efficiency: Streamlined processes minimize delays and bottlenecks, ensuring timely order fulfilment.
- Cost Reduction: Effective handling reduces damage to products and lowers labour costs.
- Space Utilization: Optimized storage solutions maximize warehouse space, allowing for better inventory management.
Functions of Material Handling
The primary functions include:
- Movement: Transporting goods within the warehouse using equipment like conveyors, forklifts, or automated guided vehicles (AGVs).
- Storage: Efficiently storing products to maximize space and ensure easy retrieval.
- Control: Monitoring and managing inventory levels to prevent overstocking or stockouts.
- Protection: Safeguarding products from damage during handling and storage.
Types of Warehouse Material Handling Equipment
Selecting the right warehouse material handling equipment is vital for operational efficiency. Here’s a comprehensive material handling equipment list:
- Conveyors: Used for transporting materials over fixed paths within the warehouse.
- Forklifts: Essential for lifting and moving heavy pallets. However, forklift-related incidents result in approximately 7,500 injuries and nearly 100 deaths annually. (wsj.com)
- Pallet Jacks: Manual or electric tools for moving pallets over short distances.
- Automated Storage and Retrieval Systems (AS/RS): Computer-controlled systems that automatically place and retrieve loads from defined storage locations.
- Cranes and Hoists: Equipment used for lifting heavy items vertically and moving them horizontally within a limited area.
Check this – 10 Types of Warehouses
Best Practices in Warehouse Material Handling
The best practices in warehouse material handling include:
1. Planning and Standardization
- Develop a Comprehensive Plan: Use a team approach to design the material handling system. (reliableplant.com)
- Standardize Equipment and Processes: Maintain consistency in the choice of equipment and operational procedures.
2. Simplification and Ergonomics
- Simplify Processes: Reduce, combine, or eliminate unnecessary movement.
- Ergonomic Design: Implement ergonomically designed workstations to minimize strain on workers.
3. Organization and Space Utilization
- Unitize Loads: Move full pallets or containers whenever possible.
- Maximize Space Usage: Implement vertical storage solutions and optimize warehouse layout.
4. Systematization and Sustainability
- Systematize Operations: Coordinate material handling across all processes.
- Adopt Sustainable Practices: Utilize reusable packaging and energy-efficient equipment.
5. Automation and Technology Integration
- Invest in Automation: Use automated picking and conveyor systems to enhance efficiency.
- Leverage Technology: Implement warehouse management systems (WMS) for real-time tracking.
6. Safety and Training
- Regular Training Programs: Conduct frequent training sessions on equipment handling and workplace safety.
- Routine Equipment Maintenance: Schedule periodic maintenance to prevent accidents and breakdowns.
7. Continuous Improvement
- Monitor Performance Metrics: Track key performance indicators (KPIs) to identify areas for improvement.
- Implement Employee Feedback Systems: Encourage workers to suggest process optimizations.
Also read: What Is Devanning & How Does It Improve Freight Handling Efficiency?
Emerging Trends in Material Handling
The emerging trends in warehouse material handling include the following:
1. Advanced Automation
Companies are increasingly integrating automated warehouse material handling equipment to improve efficiency. Robotics, AI, and automated storage solutions are revolutionising warehouses by reducing manual intervention and enhancing precision.
Automated guided vehicles (AGVs) and robotic arms are now widely used for picking, packing, and sorting tasks. By 2030, the global warehouse automation market is expected to reach $51 billion, driven by the rising demand for efficiency in logistics.
2. Autonomous Vehicles
The use of autonomous mobile robots (AMRs) and drones is reshaping warehouse operations. AMRs can independently transport goods across the warehouse, reducing reliance on human labour.
Additionally, drones are being used for inventory management, conducting real-time stock checks, and reducing manual cycle counting errors. These technologies enhance speed and reduce overall operational costs.
3. Sustainability Initiatives
Warehouses are actively incorporating green logistics practices to minimize their environmental impact. Key sustainability trends include:
- Adoption of energy-efficient warehouse material handling equipment, such as electric forklifts and conveyor systems powered by renewable energy.
- Implementation of eco-friendly packaging solutions to reduce waste.
- Use of smart lighting and temperature control systems to minimize energy consumption.
Sustainability is becoming a core business strategy, with more companies opting for carbon-neutral warehouses. The global green logistics market is expected to grow at a CAGR of 7.8% from 2024 to 2033.
4. Real-Time Data Analytics
With the integration of IoT and AI, warehouses are leveraging real-time data analytics to optimize inventory levels and improve order accuracy. Sensors and RFID tags help track material movement, reducing misplaced inventory. Predictive analytics also allows warehouses to anticipate demand patterns and adjust stock levels accordingly, ensuring seamless order fulfilment.
5. Blockchain for Supply Chain Transparency
Blockchain technology is emerging as a game-changer in material handling in logistics. By providing a decentralized and tamper-proof record of transactions, blockchain enhances supply chain transparency. It enables real-time tracking of shipments, reducing fraud and ensuring authenticity. Companies like Walmart and Maersk are already using blockchain to streamline supply chain operations.
Related read: Warehouse Automation : Types, Benefits, Trends
Challenges in Warehouse Material Handling
The challenges in warehouse material handling are as follows:
1. Labour Shortages
Warehouses worldwide are experiencing a shortage of skilled labour. The demand for workers in logistics and warehousing is growing, but a lack of training and physically demanding work conditions make it difficult to attract and retain employees.
- A report by the U.S. Bureau of Labor Statistics projects a 7% increase in material moving occupations from 2022 to 2032, emphasizing the need for workforce development. (bls.gov)
2. Rising Operational Costs
The cost of warehouse material handling equipment, labour, and energy consumption continues to rise. Fuel price fluctuations, higher wages, and increased demand for faster shipping have further contributed to financial strain on businesses. To combat this, companies are turning to automation and predictive analytics to reduce expenses and improve resource allocation.
3. Supply Chain Disruptions
Recent global supply chain disruptions, caused by events such as the COVID-19 pandemic and geopolitical conflicts, have impacted warehouse operations. Delayed shipments, material shortages, and fluctuating demand have created inefficiencies. Companies must develop resilient supply chain strategies by diversifying suppliers, adopting local sourcing, and improving demand forecasting.
4. Safety Risks and Compliance Issues
Warehouse environments pose significant safety risks, including forklift accidents, falling objects, and ergonomic strain injuries. Compliance with occupational safety regulations is critical to ensuring worker protection. To address these challenges, warehouses must:
- Implement regular safety training programs for workers handling material godown operations.
- Conduct routine inspections and maintenance of equipment.
- Use wearable safety technology, such as exoskeletons and smart helmets, to monitor worker health and prevent injuries.
5. Inefficient Space Utilization
Many warehouses struggle with inefficient storage layouts, leading to wasted space and difficulty in material retrieval. Without proper space optimization techniques, businesses experience slower order processing and higher operating costs. Solutions include:
- Implementing vertical storage systems to maximize available space.
- Using automated storage and retrieval systems (AS/RS) to reduce the footprint of traditional shelving.
- Organizing inventory based on demand frequency to improve accessibility.
6. Integration of Legacy Systems with Modern Technology
Many warehouses operate on outdated systems that struggle to integrate with modern warehouse material handling equipment. Transitioning from traditional processes to digitalized workflows requires significant investment and change management. Companies need to:
- Upgrade to cloud-based warehouse management systems (WMS) to centralize data and streamline operations.
- Adopt Internet of Things (IoT) solutions to enable real-time tracking and monitoring.
- Ensure scalability of automation solutions to accommodate future growth.
WareIQ: Redefining E-Commerce Fulfilment
Regarding multi-channel fulfilment solutions, WareIQ stands out as a trusted partner for businesses of all sizes. Y-Combinator-backed eCommerce full-stack platform offering multi-channel fulfilment across D2C, Marketplaces, Quick Commerce, and B2B (General Trade & Modern Trade).
Why Choose WareIQ?
- Pan-India Network: We operate a vast network of Seller Flex and FAssured complaint centres in over 12 cities, ensuring efficient last-mile delivery across more than 27,000 pin codes.
- Multi-Channel Fulfilment Platform: With plug-and-play integrations for major marketplaces like Amazon, Flipkart, and Myntra and D2C platforms such as Shopify and Magento, our platform supports seamless fulfilment across distributors and flagship stores. Advanced analytics capabilities help assess operational performance effectively.
- AI-Led Inventory Management: Our Inventory LogIQ solution minimises stockouts and automates replenishment, ensuring optimal inventory levels.
- Tech-Enabled Returns Management: We provide a sophisticated returns quality control solution that captures and stores media evidence of returned products, helping eliminate marketplace claim rejections.
- Comprehensive Seller Support: Benefit from dedicated account management, assistance with APOB/PPOB registrations, GST registration, and verification processes for NDR & COD.
For businesses looking to scale their operations and enhance customer satisfaction, WareIQ offers a reliable, tech-driven solution. Learn more at WareIQ’s website.
Related – Digital Warehouse: Transforming Storage Solutions
Summing Up
Optimising warehouse material handling is crucial for enhancing efficiency, safety, and cost-effectiveness in supply chain operations. Implementing best practices such as automation, ergonomic design, and real-time analytics can significantly improve productivity.
Additionally, keeping up with industry trends and overcoming operational challenges ensures a competitive edge. Businesses that invest in cutting-edge material handling techniques will not only reduce costs but also enhance overall warehouse performance.
Also read: Warehouse Services: Streamlining Operations and Costs
FAQs on Warehouse Material Handling
What is warehouse material handling, and why is it important?
Warehouse material handling refers to the movement, storage, control, and protection of goods within a warehouse. It is crucial for improving efficiency, reducing operational costs, and ensuring worker safety in logistics and supply chain operations.
What are the different types of warehouse material handling equipment?
Common warehouse material handling equipment includes forklifts, conveyors, pallet jacks, automated storage and retrieval systems (AS/RS), and cranes. These tools help streamline the movement and storage of goods while improving productivity.
What are the best practices for warehouse material handling?
Best practices for warehouse material handling include optimizing warehouse layout, using automation, ensuring proper staff training, implementing real-time inventory tracking, and maintaining safety protocols to prevent workplace accidents.
How does automation improve warehouse material handling?
Automation in warehouse material handling enhances efficiency by reducing manual labour, minimizing errors, and increasing speed in tasks like picking, packing, and sorting. Technologies such as AGVs, robotic arms, and AI-driven inventory systems improve overall warehouse operations.
What challenges do businesses face in warehouse material handling?
Key challenges in warehouse material handling include labour shortages, rising operational costs, supply chain disruptions, inefficient storage utilization, and maintaining safety standards. Implementing automation and optimised warehouse strategies can help overcome these challenges.