Unveiling the Functionality of a Typical Inventory Model
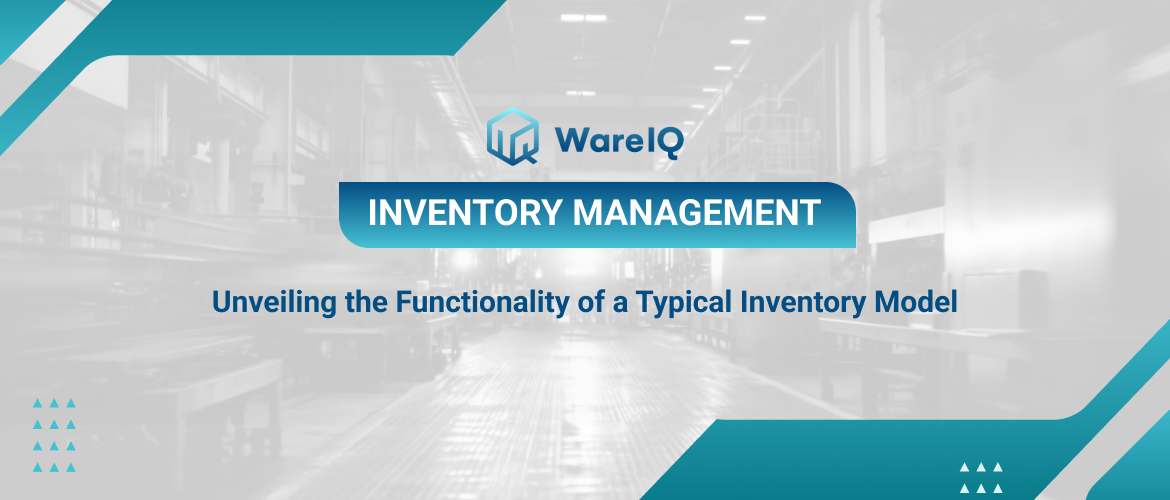
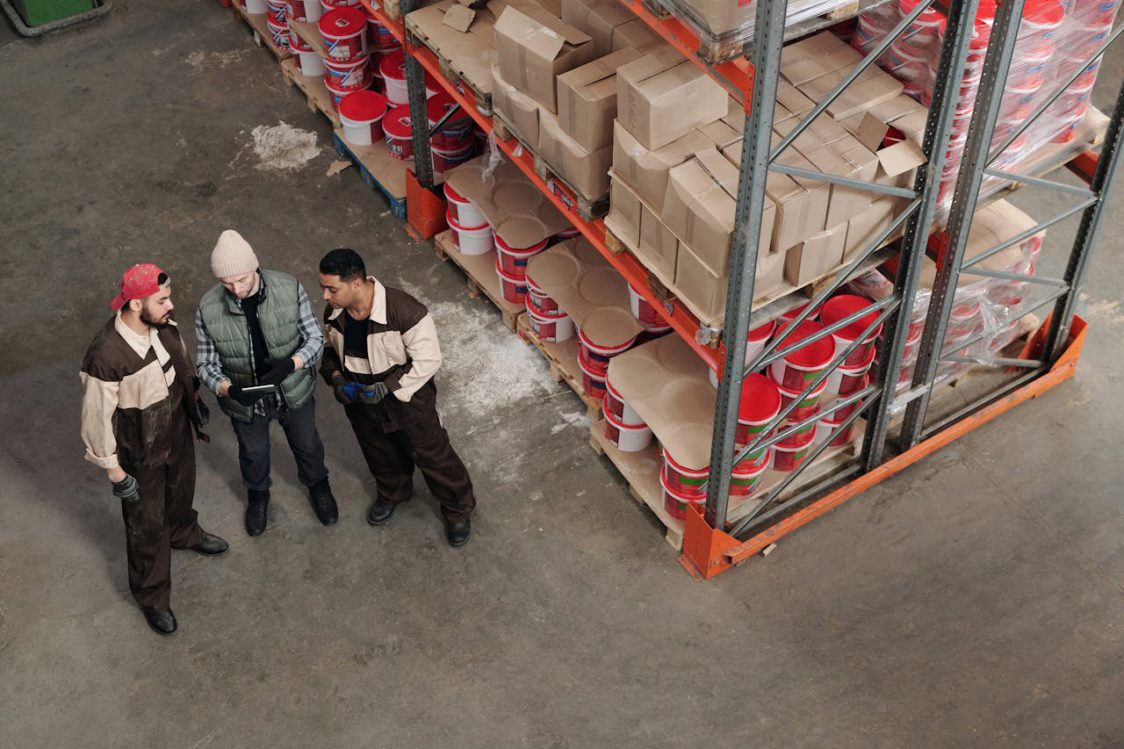
Inventory management is central to maintaining sufficient stocks while controlling the flow of costs. But can we determine exactly how much inventory to hold at any given time? If we can, then all organisations can benefit from the wisdom of how to stock and maintain. That is what inventory models or inventory control models are about.
They seek to determine a business’s exact inventory to meet customer demands, sell in the marketplace, and avoid stockouts. It also means there are no excess stocks. In this blog post, we will examine the details of inventory models, including types and examples. Finally, we will assess which inventory control model might suit your business.
What is an Inventory Model
In simple terms, inventory management is keeping the right stock at the right levels, at the right time, in the right place, and at the right costs. Inventory management models use mathematical models to concretise these operations. They enhance existing inventory systems while increasing the efficiency of poor systems.
Inventory control models start by identifying the issue. It can be a need for proper inventory management software, human error, and supply chain disruptions. Market demand and economic factors can also influence an organisation’s inventory levels.
Inventory management models provide precision by identifying selling items, necessary stock levels, and required quantities. With this information, businesses can reduce operational costs, lower storage expenses, and save money.
Types of Inventory Models
Poor inventory management can result from all sides. Some are static, like supply chain disruptions, staff unavailability, storage costs, or lack of communication. However, factors like demand surges and economic factors are not static. Accordingly, inventory management models are either deterministic or probability-based.
Deterministic models assume that the factors behind inventory management are static, while probabilistic models work based on variable factors. While the latter is more realistic, deterministic inventory models are useful in maximum business cases to give practical results.
The eight types of inventory models are:
- Economic Order Quantity (EOQ)
- ABC Analysis
- Inventory Production Quantity
- Reorder Point Model
- Fixed Order Quantity
- Safety Stock
- Just-in-Time
- Inventory Turnover Ratio
Whatever the inventory model, it should answer the following questions:
- What is the appropriate amount of inventory to order?
- Where can I reduce costs?
- Which inventory items are selling quickly?
- How much deadstock do I have?
- Which inventory is raising my holding costs?
Economic Order Quantity (EOQ)
The most dreaded part of inventory management is controlling costs while avoiding stockouts. As the name suggests, the Economic Order Quantity (EOQ) model aims to reduce costs. The EOQ calculates the best amount of items a business should order. It minimises costs and maximises value when restocking.
The formula for EOQ in inventory management:
EOQ = √2DSC/c
D = Annual Demand
C = Carrying Cost
S = Ordering Cost
Example:
A company sells 1000 mobiles a year. The annual holding cost per mobile is $5, and order placement cost is $2. Now the EOQ for the case is,
EOQ= √2*1000*2/5, which is approximately equal to 28.3.
By keeping inventory slightly more than 28 units, companies can keep costs at a minimum while meeting demand.
The EOQ model assumes a consistent demand for an item and availability for restocking. It doesn’t account for seasonal or economic fluctuations. Staying true to the nature of the model, EOQ considers fixed costs of inventory units, ordering charges, and holding charges; there is no place for stockouts.
However, the EOQ model requires continuous monitoring of stock levels. It is the most basic model based on a one-item business. Though it can be applied to multiple items in a company, it doesn’t allow correlation between them. It also needs to consider the limitations of capital availability.
ABC Analysis
The ABC inventory model seeks to optimise stock levels by assigning priorities to different items. By knowing the most significant product at a time, businesses can allocate funds accordingly. Stocks are sorted into A, B, and C categories based on the 80/20 principle, also known as the Pareto principle.
Category A: Inventory in this category gets the most cash but is only a small part of a business’s total stock. It accounts for 20% of the stock and brings 70% of the revenue. With tight inventory controls, the “A” type stock gets the highest priority.
Category B: Stock that is not essential for a business’s survival but holds importance comes under the “B” type inventory. It represents 30% of your inventory and contributes 25% of your revenue.
Category C: The type “C” represents 50% of the items with only 5% income. While it doesn’t yield as much profit as Categories A and B, it maintains stability. Inventory management for “C” is relatively simple due to its lower revenue generation.
Inventory Model Example:
For instance, in a company, A items could include specialised equipment, B items could be office supplies and C items might be consumable office stationery. Based on ABC analysis, the priority is assigned to A items.
ABC analysis is viable for dynamic organisations where items constantly change costs. However, accurately identifying the most significant stock can be daunting and result in unintended cash flows. For best results, it is often used in conjunction with the JIT model.
Inventory Production Quantity
Inventory or Economic production quantity (EPQ) augments the EOQ model. The inventory production quantity model reveals the number of items they should order in a single batch to reduce holding and setup costs. It assumes the provider delivers each order in parts rather than one full shipment.
The inventory model formula for production quantity is,
EPQ=√2KD/h(1-x)
K =Ordering/Setup cost per production run
D = Annual demand rate
h = Annual holding cost per product
t = Cycle length
P = Annual production rate
x=D/P
Inventory Model Example:
Annual demand = 15,000
Setup cost = $500 per production run
Holding cost = $50 per item per year
Number of working days per year = 240
Annual production rate = 25,000
x=0.6
EPQ= √2*15000*500/50(1-0.6), which is equal to 866.02 (rounded).
The company must order 866 units in a single batch for optimal inventory costs.
Reorder Point Model (RP)
The Reorder Point inventory control model determines the inventory level at which a new order should be placed to maintain optimum stock levels. Based on lead time and average demand, stock levels are ensured until the next shipment time.
Inventory model formula for Reorder Point:
Reorder Point= Supply Lead Time x Average Daily Demand
RP Inventory Model Example:
Lead Time = 10 days
Average Daily Demand = 40 units/day
Reorder Point= 10×40=400 units.
So, the company should order when the inventory level drops to 400 units
Fixed Order Quantity
This model is the most basic inventory control system. It seeks to identify the fixed order based on a fixed inventory level. The order quantity is determined using the EOQ model, and the reorder point is calculated using the Reorder point model.
Example:
EOQ = 490 units
Safety Stock = 295 units
Average Daily Demand = 40 units/day
Lead Time = 10 days
The reorder point is 400 units in inventory (calculated using the reorder point model). Whenever the reorder point comes, order 490 more units.
Safety Stock
Safety stock is a buffer to guard against demand and lead time uncertainties. It ensures product availability during unexpected changes.
Inventory model formula:
Safety Stock Level= (Maximum daily use x Maximum lead time) – (Average daily use x Average lead time).
Example:
Suppose a company sells an average of 10 products daily, with a 14-day lead time. During peak periods, sales reach 15 products daily, and lead time extends to 18 days.
Then the safety stock is (15 × 18) – (10 × 14), which is 130 units.
Just-in-Time Model
JIT focuses on reducing inventory expenses by scheduling production or ordering goods precisely when they’re needed, eliminating stockpiling. So, there is no mathematical formula for the JIT inventory control model. It is a qualitative method that synchronises production and ordering with demand. It can be a general rule that ultimately saves inventory costs significantly.
Inventory Turnover Ratio
The inventory ratio establishes a relationship between the average inventory and the Cost of inventory sold during a particular period. It uses the following formula:
Inventory Turnover Ratio=Cost of Goods Sold/Average Inventory
Average inventory is ideal when merchandise fluctuates greatly throughout the year. Comparing the inventory ratio of successive years reveals fast-moving items, slow-moving items, and items with zero demand.
Probabilistic Inventory Models
Probabilistic inventory methods offer more reliable results than deterministic approaches. They acknowledge demand fluctuations and lead time uncertainties. Three common scenarios exist:
- Constant lead time with variable demand
- Constant demand with a variable lead time
- Variability in both
However, more complex models with multiple variables also exist. Using economic and production data, it estimates inventory quantities and their probabilities.
In most cases, probabilistic inventory models considering both probabilistic supply and demand are preferable. There are two methods for procuring inventory stock based on how often orders are placed: single-period and multi-period inventory systems.
Single Period Inventory Model
The single-period inventory control model assumes that items are perishable. They are ordered once and are in limited demand, such as seasonal products like newspapers or winter clothes. It applies an incremental analysis to find the best order quantity by comparing the Cost of one more unit against the Cost of not ordering it. A probabilistic demand is assumed for calculation.
Multi-Period Inventory Model
A multi-period inventory or continuous review inventory model involves constant monitoring. When stock hits a set level, a fixed amount is ordered. This model suits high-volume or crucial inventory items.
Periodic review inventory is checked at set intervals, regardless of stock levels. The orders are made to reach maximum levels. This method suits moderate-volume items.
How to Choose the Best Inventory Model for Your Business
- For businesses with consistent demand, the EOQ inventory model is the best. It balances both order quantity and storage costs.
- When lead times are unpredictable, use the safety stock formula to calculate the best inventory level without running into stockouts.
- ABC analysis works best for businesses with a broad product spectrum, varying costs and sales volume.
- Apply the Just-in-Time model for companies with perishable or low shelf-life items. It is the best bet to minimise inventory costs and overstock.
- Companies with limited funds may use fixed order quantities for vital items and Just-in-Time (JIT) for less important products.
- For businesses with storage space limitations, prioritise the fast-moving items and use the JIT model. Dropshipping is also the best alternative.
- The Reorder point model, in combination with Safety stock, is the best for businesses that deal with unreliable suppliers to keep inventory costs at a minimum.
- Before finalising a model, it’s smart to confirm the choice with industry experts or through trial testing.
- Growing businesses can only cram some models to determine the best inventory levels. Try multiple methods one by one and start evolving in the application. There is no hurry!
Related read: Change in Inventory Formula
Conclusion
Inventory management models serve as a tangible resource for companies to control costs and prevent stockpiling and stockouts. However, what is the best inventory model for a business? That takes wisdom and iterations. More complex inventory control models may be used for tight control. Ultimately, the choice depends on demand forecasts, order lead time, and review frequency.
FAQs
What are the four inventory models?
The four basic inventory models are Economic Order Quantity (EOQ), ABC analysis, Economic Production Quantity (EPQ), and Reorder Point.
What is the best inventory model in operation research?
Economic Order Quantity (EOQ) for constant demand, (s, Q) for continuous review, (R, S) for periodic review, Newsvendor for perishables, and Multi-Echelon models for supply chains are some of the best inventory models in operation research. Every model gives the best results by identifying the problem and selecting the trade-offs.
What does a typical inventory model address?
A typical inventory model should answer the following questions:
What is the appropriate amount of inventory to order?
Where can I reduce costs?
Which inventory items are selling quickly?
How much deadstock do I have?
Which inventory is raising my holding costs?
How do probabilistic inventory models differ from deterministic models?
Probabilistic inventory models consider variable situations for demand, lead time, and orders, giving more realistic results. However, deterministic models consider static factors such as fixed demand, lead time, or fixed orders per period. Despite their basic nature, deterministic models are useful in several cases.
How to choose the best inventory control model for my business?
The best inventory control model depends on demand variability, lead times, products, service level requirements, and cost minimisation objectives.