What is MRP: Mastering and Optimizing Your Supply Chain
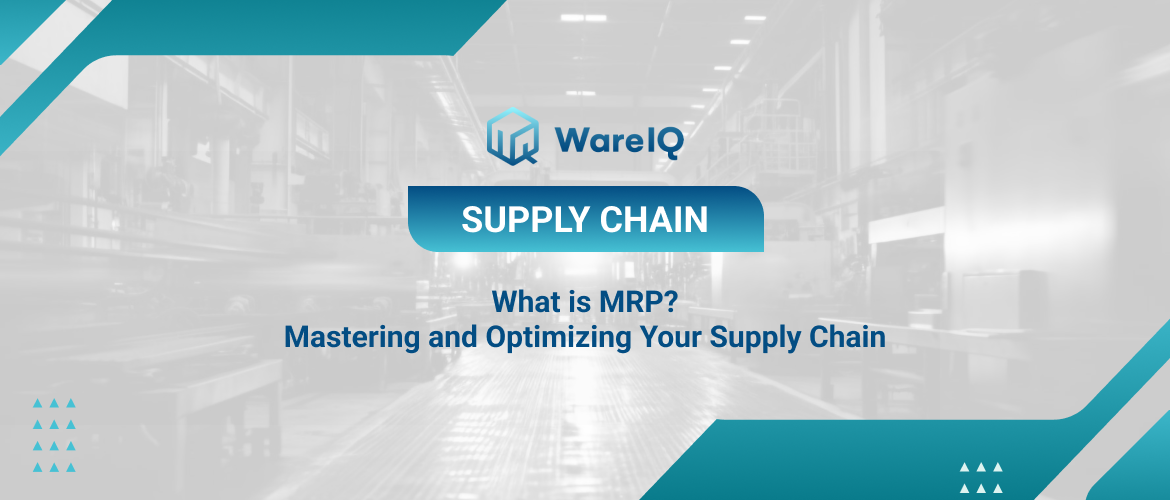
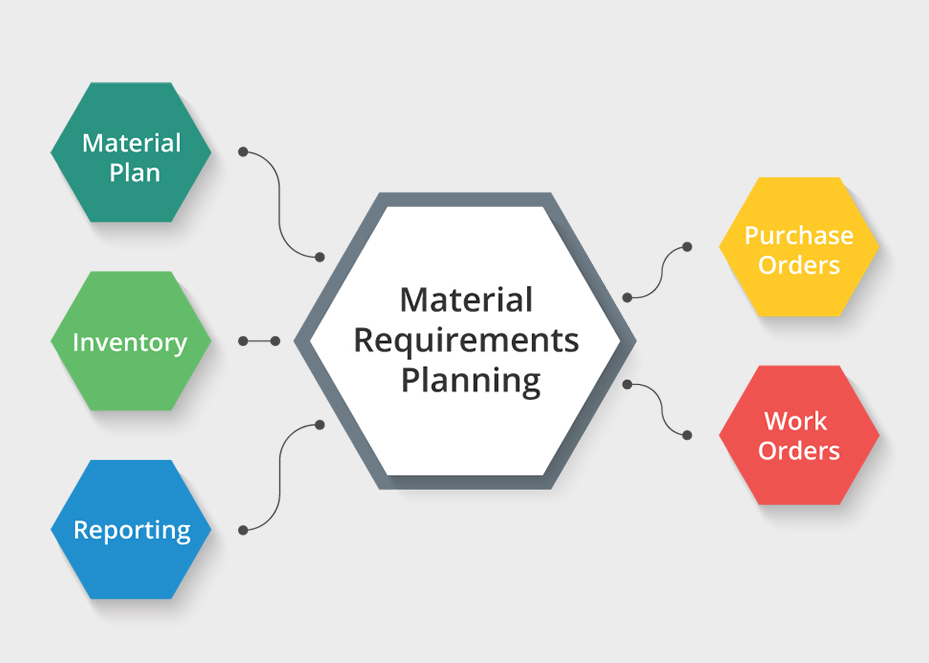
A technique called material requirements planning (MRP) determines the materials and parts required to make a certain product. It consists of three main steps: listing the materials and components already present, deciding which more are required, and then planning for their manufacture or acquisition.
Importance of Material requirement planning
- MRP, which is generally carried out using specialised software, aids in ensuring that the proper inventory is accessible for the manufacturing process precisely when it is required and at the lowest cost.
- Material requirements planning boosts the productivity, adaptability, and profitability of manufacturing processes in this way. It can increase worker productivity, enhance product quality, and reduce material and labour costs in factories.
- Additionally, material requirements planning enables businesses to adapt more swiftly to escalating demand for their goods, avoiding production snags and inventory stockouts that may cost them clients, ultimately resulting in revenue growth and stability.
- MRP is extensively employed by manufacturers and has certainly played a significant role in the expansion and widespread availability of consumer products at reasonable prices, which has enhanced the quality of living in most nations.
- It is improbable that individual firms could have scaled up operations as quickly as they did in the 50 years since the introduction of material requirements planning software without a mechanism to automate the intricate calculations and data management involved in material requirements planning procedures.
Information used by MRP
Aspect | Description |
Product Names | Unique product names or “independent demand” plans for accuracy and organization. |
Orders | Utilizes current orders and sales forecasts with details on quantities, customer deadlines, and product orders. |
Inventory | Integrates existing inventory systems, specifying finished products, available materials, and expected supplies. |
Materials | Lists materials, equipment, shelf life, and storage conditions for production. |
Timeline | Includes production process durations and requirements for machinery and team members. |
Constraints | Considers machinery capacity, business infrastructure, team members, and quality/testing standards. |
Top Features of MRP
Demand forecasting
- Demand planning and forecasting is a significant material requirements planning component since it is used to establish the kinds and amounts of materials needed for production based on either existing or expected demand.
- The key to preventing possible inventory problems, such as creating too many or too few things within the needed time frame, is accurate demand forecasting.
- By doing this, you’ll be able to keep your inventory-holding expenses to a minimum and fill orders on time.
Planning
- The main focus of material requirements planning is planning, namely the acquisition and sourcing of raw materials required to meet incoming demand.
- Giving your buying department a better understanding of what is required to finish a work, whether it has been purchased or is being predicted, is one of MRP’s main objectives.
- You may make sure you have adequate materials on hand by making a list of all the things you’ll need, along with the amounts that are needed.
- Manufacturers should look at material requirements planning software with this feature since purchase planning is a crucial part of planning and scheduling.
Scheduling
- You must schedule your production once the necessary supplies and stock have been identified and purchases have been completed.
- In this stage, you’ll examine how long it will take to execute your manufacturing orders as well as the resources and manpower that will be needed.
- To make sure that you can order your supplies and receive them in time for production, it is essential to use production scheduling software that can create a defined timetable.
Benefits of MRP
- Inventory Management: For production efficiency to be realised, inventory management is essential. material requirements planning systems use information from the production schedule to calculate the precise quantity and price of inventory needed to fulfil demand. MRP systems keep the right amount of components and materials in stock, which lowers the cost of carrying inventory. This lowers and optimises the cost of inventory throughout the course of a manufacturing period.
- Monitoring: Knowing what is available, what to purchase, and when to get it is crucial for streamlining the manufacturing process. A smart system is needed for buy planning in order to monitor the production processes, detect any purchases that are required, and double-check the production schedule and anticipated material deliveries. When a purchase is necessary, procurement managers set up MRPs to automatically contact vendors.
- Rerouting: Material requirements planning systems identify production line bottlenecks brought on by a shortage or a drop in material. When this occurs, the system can advocate rerouting production to the manufacturing of a new product where supplies are available, or it can reroute production itself. MRPs might concentrate efforts on one stage of the production process at the expense of another step that lacks the necessary raw materials and components. Even when there are limitations on the availability of materials, MRPs assist producers in planning their production lines.
- Scheduling: Work scheduling controls the amount of time that is spent in active production, forecasting projected yields, and ensuring production schedule conformance. Using the given inventory, MRPs depict the overall manufacturing process. Managers may precisely anticipate labour time and operational expenses using this data, as well as regulate hourly operations, equipment usage, and labour-intensive jobs.
- Availability of resources: Any industrial process depends on its raw materials. The manufacturer has a better understanding of additional resources available to use in the process when they have control and fast access to information about the availability of raw materials and predicted yield. Here, efficiency is crucial. The material requirements planning system provides the manufacturer with information on when extra labour is needed, what equipment is needed at what time, and whether to hire or purchase operational assets.
- Data management: A huge quantity of data is produced, examined, and presented during the manufacturing process. material requirements planning systems offer support to manufacturers in managing this data. MRPs process and record data from purchases, inventories, deliveries, and cash flows into invoices, lists, reports, receipts, and other conveniently arranged displays.
- Economic: The method determines the most economically feasible purchase to meet demand by factoring in the amount and cost of items required, including the cost of shipping, storage, and transporting. material requirements planning systems accurately and economically optimise purchases, saving the company money on unneeded purchases.
- Time management: Material requirements planning systems are fully automated and require little human intervention. This saves a great deal of labour time otherwise used to do inventory, purchases, and production management. The level of accuracy in these systems is far beyond any error-prone human method. It also manages and stores production data, which eliminates the need for entire departments.
Material Requirements Planning Process
Step | Description |
Select MRP System Software | Choose MRP software tailored to business needs, considering unit conversions, cost tracking, and traceability functions.Evaluate supplier’s services, system integration with existing accounting and inventory systems, and post-sale support. |
Install and Test Software | Install selected material requirements planning software and test it to ensure it meets expectations.Perform test tasks aligned with business objectives.Create an implementation plan with the start date and user access details. |
Audit and Analyze Data | Decide which data the material requirements planning system will use, including raw materials, product specs, and order volumes.Verify data accuracy and consistency against existing records.Check demand against inventory and calculate production times and deadlines. |
Train Team Members | Ensure that all personnel involved in production understand how to use the MRP software.Provide interactive instructor-led training and offer printed or electronic manuals.Implement periodic training to keep team members updated on software changes. |
Monitor and Report | Continuously monitor the MRP system to make adjustments and address issues.Check details like order quantities and scheduling information to prevent delays.Generate analytical reports to improve software usage and production processes. |
FAQs
What does MRP stand for?
MRP stands for Material Requirements Planning.
How does MRP software benefit manufacturing processes?
MRP software enhances productivity, adaptability, and profitability in manufacturing by optimizing inventory, improving product quality, and reducing costs.
Why is accurate demand forecasting essential in MRP?
Accurate demand forecasting is crucial to prevent inventory problems and ensure on-time order fulfilment.
What are the main steps in the Material Requirements Planning (MRP) process?
The main steps in MRP include selecting software, installing and testing it, auditing and analyzing data, training team members, and monitoring and reporting.
How does MRP contribute to cost savings in manufacturing?
MRP systems optimize inventory management, procurement, scheduling, and resource allocation, resulting in cost reductions and efficient use of resources.