What are Inbound And Outbound Logistics? Top 7 Ways To Optimize Inbound And Outbound Logistics Processes [Ultimate Guide 2025]
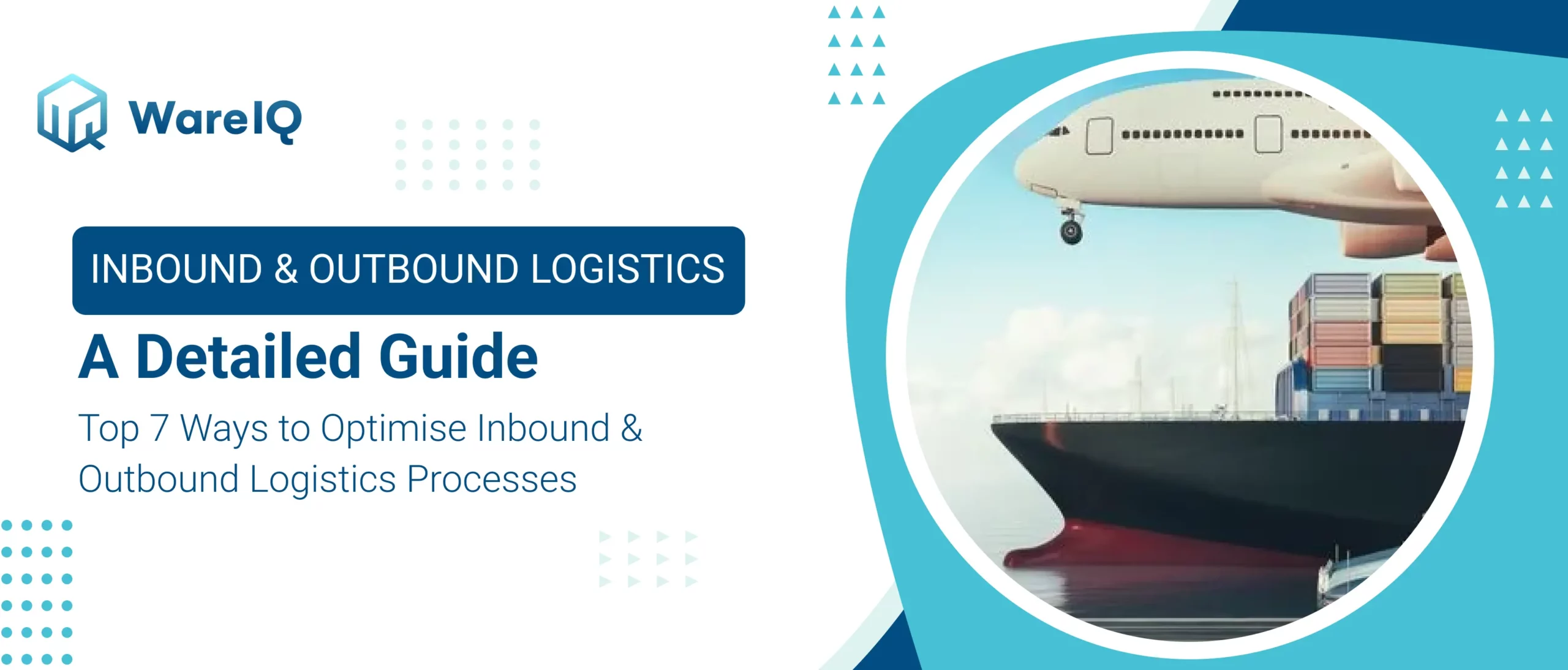
In the 21st-century economy, firms battle for efficiency. Whether it is inbound and outbound logistics, marketing, finance, or another area of the business, it is survival of the fittest. Since the dawn of the industrial era, logistics has been subject to continuous improvement, and optimization always pays off, especially when it comes to inbound and outbound processes. Better ways of procuring materials, and better ways of distributing products contribute to an efficient firm and a healthier bottom line. This process is related to the concept of supply chain management (SCM).
Generally, inbound logistics and outbound logistics work in sync to create a better supply chain. Manual inbound and outbound logistics management processes are important. Technology has changed the rules of the game. A mixture of machine learning, AI, and complex algorithms are now used to ensure better eCommerce logistics management.
- What is Inbound Logistics?
- What is Outbound Logistics?
- Inbound and Outbound Logistics: 4 Key Differences
- Inbound Logistics Processes: 3 Steps To Success
- Outbound Logistics Processes: 4 Steps To Success
- 5 Most Prominent Inbound And Outbound Logistics Challenges faced in 2025
- 7 Ways to Optimize Inbound and Outbound Logistics in 2025
- Conclusion
- Inbound and Outbound Logistics Process FAQs
What is Inbound Logistics?
Inbound logistics is the means by which materials and other products are obtained by a firm which encompasses all the activities that are involved such as ordering, receiving, storing, transporting and managing the goods. Inbound logistics is focused on the supply aspect of eCommerce.
Examples of Inbound Logistics Procedures
- Sourcing of Materials and Goods: This includes choosing prospective vendors, getting pricing estimates and negotiating with suppliers.
- Placing Orders: This includes purchasing the relevant materials that the retailer needs for operating their business.
- Transporting Products: This involves figuring out which transport method would be the best option, partnering with 3PL logistics companies and finding the quickest routes.
- Receiving the Goods: This involves unloading the cargo and receiving the goods so they can be stored.
What is Outbound Logistics?
Outbound logistics entails the storage and transportation of products to their relevant locations and all the processes involved in it such as picking, packing, delivery and customer support. Outbound logistics focuses on the demand aspect of eCommerce.
Examples of Inbound Logistics Procedures
- Warehouse Management: This involves the use of a WMS to automate and streamline various warehouse processes such as picking, packing labelling of orders.
- Inventory Management: This involves managing inventory in the warehouse so it can be stored in the most efficient and accessible manner and doesn’t take up unnecessary space.
- Order Dispatch: This involves the transport of goods from the warehouse to the storage hub in the same city where the order needs to be delivered.
- Last-Mile Delivery: This involves the order being picked up by a delivery executive so that it can be successfully delivered to the final customer.
Inbound and Outbound Logistics: 4 Key Differences
Both inbound logistics and outbound logistics are key to product quality and customer experience. Efficiency in these inbound and outbound processes is essential for a business’s success. This post, therefore, is a pointer to both the inbound process in the fulfillment warehouse and the outbound processes and their optimization.
Inbound Logistics | Outbound logistics |
---|---|
The process of inflow of raw materials into a business’s manufacturing plant is called inbound logistics. | The process of outflow of the finished (manufactured) product to end-users is called outbound logistics. |
The activities involved in inbound logistics are: 1. Raw material sourcing 2. Storage of raw materials 3. Delivery of materials to be used in production | The activities involved in outbound logistics are: 1.Packaging of finished goods 2.Transportation and distribution of finished goods 3. Customer service |
Inbound logistics is the relationship between a business and its suppliers. | Outbound logistics is the relationship between a business and its customers. |
Inbound logistics focuses on material management and production. | Outbound logistics focuses on distribution and customer service |
Read on to understand how to tune inbound and outbound logistics to avoid wastage, delays, and overall inefficiencies.
WareIQ, an eCommerce fulfillment company, empowers online brands with a superior-tech platform to compete with Amazon like service levels by bringing their average delivery timelines from 5-10 days to 1-2 days.
Inbound Logistics Processes: 3 Steps To Success
Fine-tune these 3 steps for an optimized inbound logistics process:
- Sourcing of Raw Materials
- Receipt of Goods
- Reverse logistics
Sourcing Of Raw Materials
The first step in the manufacturing of goods is the sourcing of raw materials. Businesses need to buy raw materials of good quality in the right quantity from trusted suppliers. A key process here is maintaining records of raw materials so that overstocking of raw materials is avoided. Maintaining good communication with suppliers is essential. Coordination with suppliers and setting a transportation framework is an essential parts of the inbound logistics process in the warehouse.
Receipt of Goods
The optimal receipt of goods involves careful planning. After placing an order for raw materials with the supplier, the business needs to make advance load appointments. Docks need to be reserved for the unloading of inventory. By doing this, businesses know where to receive raw material stocks when they arrive. The unloading area should be assigned and inventory should be unloaded and stored in the designated area for a short period of time.
Reverse Logistics
When goods are moved from the end-user/customer back to the manufacturer, the process is referred to as reverse logistics. This is an essential part of the modern inbound logistics process in the warehouse. The return of goods to eCommerce firms and refurbishing, remanufacturing, or disposing of products are part of this process and are handled by reverse logistics companies.
Outbound Logistics Processes: 4 Steps To Success
Fine-tune these 4 steps for an optimized outbound logistics process:
- Order Processing
- Picking and Packing
- Shipping and Sorting
- End-User Delivery
Order Processing
The outbound logistics process begins with the customer placing an order, which is then confirmed by the warehouse. A Warehouse Management System (WMS) is used to streamline this process and mitigate any errors that could have otherwise occurred.
Picking and Packing
After order confirmation, the ordered product is picked from the inventory. Meanwhile, in the background, the WMS updates inventory records and adjusts the product count and SKUs. These products are then packaged and labeled (you can read about shipping labels here). The carrier service sorts out these products.
Shipping and Sorting
After packing and sorting, the goods are picked up by freight trucks, which ship them to the pertinent distribution center. After the goods have reached the closest distribution center (to the customer), the orders are picked up by the relevant delivery personnel. This process is carried out by shipping companies.
End-User Delivery
End-user delivery is the last step that finishes off the inbound and outbound processes of logistics. Whether the delivery is to an individual or a supermarket, this end-user delivery is the final step of the inbound and outbound logistics chain.
5 Most Prominent Inbound And Outbound Logistics Challenges faced in 2025
Knowing the challenges that businesses could face in the field of logistics gives retailers a handle on how to deal with them. These are the top 5 challenges in inbound and outbound logistics processes.
Poor Knowledge of Transportation Status
Revenue, efficiency, and productivity of a business can be affected by poor visibility of the product through the logistics process. Inbound and outbound processes in logistics involve multiple transacting stakeholders. This makes poor visibility a huge challenge.
The status quo is the low visibility of transportation operations. Not knowing the execution status of orders results in inefficient planning and a poor customer experience. If stakeholders aren’t in the knowledge loop at various stages of the delivery process, it may result in an inefficient transaction.
To stay on top of the game, firms need to notify customers of the transportation status of the ordered goods from the time of order placement up to the delivery, in real-time.
High Operational Costs
Transportation of ordered goods is one of the highest costs that factor into the purchase price. The cost of this process is steadily rising. The reasons for this high cost are:
- Rising fuel prices
- Management and administration costs
- Poor visibility
- Poor coordination
- Several transportation modes
These operational costs are usually passed down to the customer and are an important factor in customer satisfaction.
Inefficiency in Internal Operations
When plant operations are sub-optimized, i.e. inefficient, it negatively impacts the overall business revenue. These inefficiencies could be any of the following:
- Inaccurate inventory data
- Inexperienced manpower
- Poor handling of materials
- Wastage
- Inefficient input of products
Such inefficiency results in sub-par products and a poor customer experience. Business profits dive, competitiveness decreases, and goodwill is reduced.
Mismanagement of Delivery Fleet Resulting in Low Productivity
In today’s hyper-competitive market, products need to be delivered on time, every time. Sometimes it is the delivery fleet that is the problem. The areas of concern in the delivery fleet could be:
- Poor vehicle maintenance
- Unoptimized route planning
- Too many stoppages
- Bad driver performance
Not handling these issues could mean delayed deliveries, higher operational costs, lowered customer trust, and a decline in the goodwill of the business.
Decision-Making Based on Inaccurate Facts/Data
Broadly speaking, business decisions made based on relevant data are more likely to be sound. Making decisions without proper data is akin to playing guesswork with your finances. When eCommerce logistics companies decide on a key deliverable, such as inbound logistics processes in the warehouse without data, it may be a recipe for failure.
Data helps businesses understand the performance of various metrics in the inbound and outbound logistics chain. Risk assessment is possible only with valid data. The lack of data could also mean that core internal processes are not being performed properly.
7 Ways to Optimize Inbound and Outbound Logistics in 2025
Modern technology has simplified every area of business operations, including logistics. The vast array of digital technology now enables easy optimization in inbound and outbound logistics. The effort is to smooth out processes and decrease logistics costs while enhancing productivity. Follow these 7 ways to optimize your inbound and outbound logistics processes:
Relying on Automation
Automating logistics allows for the use of the best delivery routes. This is done using intelligent route optimization software. A mix of analytics, machine learning, GPS tracking, and dynamic routing is used to select the best routes. Productivity is enhanced due to the use of tracking various stages of the inbound and outbound logistics processes. Whether it is the unloading of goods, in-plant operations, or any other area of logistics management, businesses stand to save a lot of money by sticking to time frames.
Suggested Read: How Do Delivery Route Planning Apps Help in Delivery Route Optimisation?
Managing Advanced Logistics
Current logistics management systems allow businesses to stay up-to-date. Certain varying factors like freight charges and other dynamic factors can have a detrimental impact on inbound and outbound logistics. Stay on top of dynamic changes using advanced logistics management. Keeping your eye on current rates can save you plenty of money, time, and effort.
Providing A Better Customer Experience
By optimizing inbound logistics and giving customers end-to-end visibility of transportation operations, businesses can enhance customer experience. End-users can track their shipment at any stage of the delivery and this is an essential part of modern logistics management. By planning production and ETAs appropriately, businesses can communicate with customers without any errors. This is an essential part of an effective inbound and outbound logistics system.
Developing Vendor Inbound Compliance Standards (VICS)
Developing standards for business processes apply to all areas of business operations. It is no different with inbound and outbound logistics. Modern businesses deal with an array of suppliers and vendors. This makes streamlining business processes crucial. To do this, businesses design Vendor Inbound Compliance Standards (VICS) which are then used as guidelines by all stakeholders. These lead to a steady, uninterrupted flow of logistics.
Developing Strategic Supplier Relationships
Efficient logistics operations depend on strategic relationships built with third-party suppliers, carriers, and logistics providers. Optimizing such relationships result in efficient logistics operations. The key parameters that need to be examined for this are:
- The volume of goods delivered
- Other shipping activities
- On-time, in-full deliveries
- Pricing models
Analyzing suppliers based on these parameters is a breeze using current logistics management platforms. Businesses can know how their operations are being impacted and by which suppliers. This can then be the roadmap for future strategic relationships.
Optimizing Communication
In the world of logistics, communication equals efficiency. Inbound and outbound logistics involve multiple stakeholders. A break in communication could mean a weak link in the chain. Only an efficient communication system can ensure that goods move as per the schedule and as per plan. Both delivery personnel and warehouse managers need a way to be constantly in touch with the business headquarters. This enables quick decision-making and the easy resolution of errors. Modern logistics tools allow for optimized routes, location tracking, and hence, high transparency.
Cross-Docking Warehouse Operations
Cross-docking is an important concept in modern inbound and outbound logistics. In this practice, incoming goods are quickly sorted out by workers, which are then loaded on an outbound truck. The time spent by the products in the warehouse is reduced and this means reduction/optimization of warehouse space. Finished products can be quickly inspected. This ensures the delivery of high-quality products and a lower return rate.
Conclusion
Inbound and outbound logistics are some of the most important processes in order fulfillment. Businesses have to make sure they have a proper supply chain in place if they want their orders to be successfully delivered on time and intact. It can take a lot of time and resources for smaller businesses in trying to optimize these processes to be as efficient as possible. This is where 3PL fulfillment companies such as WareIQ can help.
Explore more on Types of Logistics
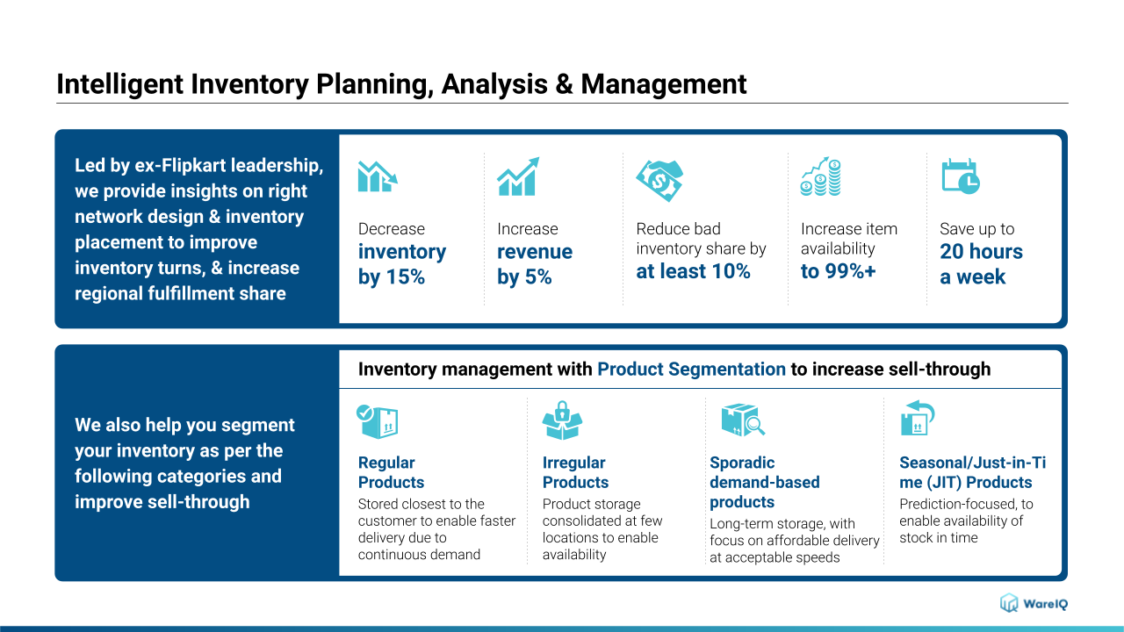
WareIQ provides services for all inbound and outbound logistics processes in logistics, freeing up the time and effort needed by businesses for other tasks such as optimizing their business strategy and refining their products. We take care of the entire process of order fulfillment, from receiving orders through our custom WMS to offering ultra-fast same-day and next-day delivery to customers.
- Pan India Fulfillment & Darkstore Network: Plug-and-play fulfillment infrastructure with no minimums, which is compliant with Amazon Seller Flex, Flipkart Assured, Myntra and other marketplaces
- Inventory & Network Planning Excellence: Best-in-class AI models for sales forecasting, product segmentation, and inventory management to reduce inventory by 40% and increase revenue by 10%.
- Vertically Integrated Fulfillment Tech Stack: Our Fulfillment Tech Solution supports integrations with 20+ top marketplaces & D2C platforms, and prominent national, regional and hyperlocal couriers, enhancing reach by covering deliveries for 27,000+ pin codes
- Supply Chain Productivity Applications: Integrate a host of supply chain productivity apps with a single-click to your existing CRMs, ERPs & accounting software to manage your logistics workflows from one command center. Use Apps like RTO Shield to get 100% RTO protection, Branded Tracking to turn your order tracking page into a profitable marketing channel, and many more.
Trusted by 300+ top Indian brands, we are helping them accelerate online sales and expedite their growth through a synergistic combination of advanced technology, robust fulfillment infrastructure & seller enablement services!WareIQ is backed by leading global investors including Y Combinator, Funders Club, Flexport, Pioneer Fund, Soma Capital, and Emles Venture Partner.