How to Reduce Transportation Costs in Distribution Networks in 2025 for eCommerce and D2C Business?
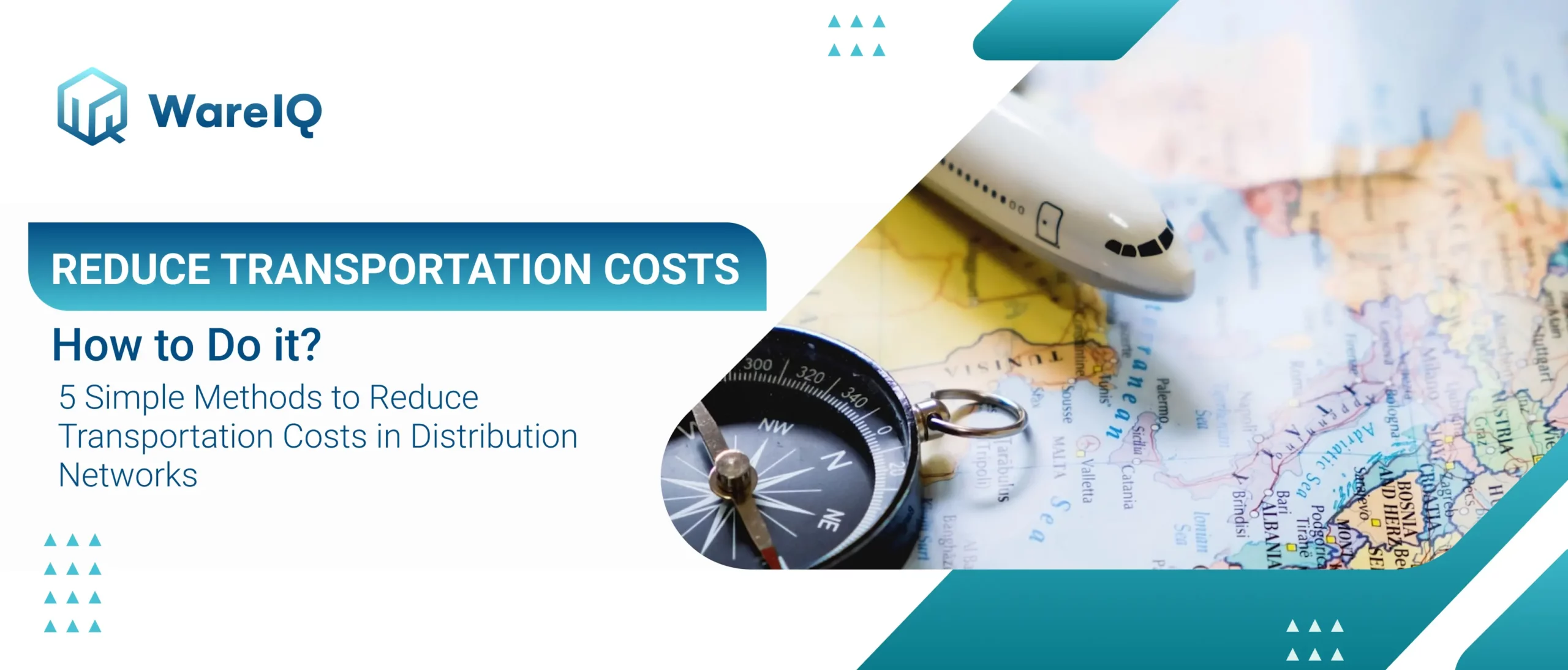
Transportation and eCommerce logistics are a vital part of a company’s eCommerce operations as they enable goods to be successfully delivered to the customers that ordered them. Companies today are embroiled in stiff competition as they try to outdo each other in terms of who can provide the fastest and cheapest possible delivery to customers so that they do not need to incur additional shipping charges. However, this could also have a negative as these costs may fall onto the shoulders of the companies themselves, which could ultimately reduce their profit margins.
While efficient transportation is a must for any self-respecting eCommerce company, they also need to find the sweet spot between good service and ways to reduce transportation costs in their distribution. In this blog, we’ll be discussing just that, in addition to what transportation costs in eCommerce are and a few examples of them.
What are Transportation Costs in eCommerce?
Transportation costs in eCommerce involve any expense that goes into transporting raw materials to the supplier, transporting finished goods to their relevant fulfillment centers and warehouses, and delivering the products to their final customers. The costs involved in the management of returns and picking up the goods from customers and transporting them back to the warehouse can also fall under transportation costs as it involves the entire logistical procedure to be repeated but in reverse.
If a company is not careful in the way it manages its transportation and distribution costs, it can easily be caught off-guard by skyrocketing expenses, which can result in unforeseen delays and unfulfilled products. If a customer does not receive their product in time or is not satisfied with the overall delivery experience, it may cause them to leave negative reviews and reconsider purchasing from that company again. This is why it is important for companies to find ways to reduce transportation costs and keep them in check. Transportation costs can be calculated using the following formula:
Transportation Costs = Total Transport-Related Expenses ÷ Total Sales Revenue
WareIQ, an eCommerce fulfillment company, empowers online brands with a superior-tech platform to compete with Amazon like service levels by bringing their average delivery timelines from 5-10 days to 1-2 days.
5 Factors That Impact Transportation Costs in a Company’s Distribution Network
Fuel Prices
We live in an age where almost all major transportation networks still rely on fuel and thus, retailers are at the mercy of whatever global or local occurrences cause fuel prices to fluctuate or stabilise. Stable fuel prices allow companies to accurately gauge how much would be spent on transportation. However, as we have seen recently, fuel prices can easily fluctuate and skyrocket, which in turn, causes transportation costs in a company’s distribution network to also increase, resulting in higher prices to fulfill orders and transport goods.
Weather Conditions
Just like fuel prices, there is little to nothing a retailer can do to positively affect weather conditions in their favour. In the case of extreme weather such as excessive thunder or hail storms, most major transport facilities such as planes, ships, trains, and trucks are affected, which causes unforeseen delays and negative sentiments among customers that are waiting for their deliveries. This increases the time needed for each delivery and thus, also increases transportation costs. On-ground transportation can also easily be affected by natural calamities such as landslides, fallen trees, roads being damaged due to harsh weather, traffic pileups, and more.
Travel Distance
If you would assume that the further the destination is from the point of dispatch, the more expensive it would be to transport an item, you would be right. Sheer distance necessitates the use of more fuel, longer travel times and a generally longer waiting period for an order to be delivered.
However, to offset the challenges associated with the increasing distances needed to fulfill cross-country orders, many companies are opting to partner with 3PL warehousing companies with large warehouse networks so that they can store their merchandise closer to areas of high demand and transport their products from there which will reduce distribution costs as opposed to from a central warehouse where distances could be near or far depending on the final destination.
Total Shipment Weight
This is another instance where larger translates to more expensive. The bigger a shipment is, the more space it will take up on a vehicle, so the more expensive it is to transport. This is why companies generally prefer to ship orders in bulk, find ways to package their products to take up as little space as possible and strategically place them, so they have a reduced footprint compared to stacking them side by side. These practices aid in helping reduce transportation costs.
Related Article: How to Reduce Package Sizes?
Delivery Speed
Generally, faster delivery means more expensive delivery because more resources and planning are necessary to ship an order in a day compared to a week. Every aspect of the delivery, from the picking and packing to the shipping and last-mile delivery needs to be meticulously planned in order to achieve an ultra-fast delivery. Additionally, the order may require faster and more costly vehicles to make up time in transit. Here is how you can increase shipping speed keeping in mind the affordability.
5 Methods to Reduce Transportation Costs for Your eCommerce Firm in 2025
Consolidate Deliveries in a Single Shipment
Shipping companies generally provide discounts if the order value is beyond a certain threshold. To take advantage of these discounts and more efficiently transport products, you can club as many orders as you can into a single shipment without compromising the safety and quality of the delivery. This will enable you to reduce transportation costs as many orders can be delivered in one single shipment as opposed to many separate shipments while also making use of bulk discounts provided by the operator.
Outsource Your Warehousing Requirements to a 3PL
3PL companies generally have vast networks of warehouses and fulfillment centers, scattered across the country, which means that you can store your products closer to areas where you are getting the most demand or in proximity to major transportation hubs. This will reduce the distance that each parcel has to travel and will ultimately reduce distribution costs. Partnering with a 3PL is a good idea because their warehouses are fully stocked with all the latest technology so you do not need to worry about anything getting misplaced because every SKU and order placed can be monitored through a WMS software from wherever you are.
Utilize Automated Container Loading Systems
Loading or unloading items on or off vehicles are part and parcel of eCommerce transportation. One way to speed up the process, lower the number of errors that can occur, and reduce transportation costs, is to use an automated container loading system. It is a simple mechanism where a leading plate can slide under the container and load or unload the entire shipment in a single attempt. Using it will allow you to shorten the amount of time that is needed, reduce the amount of labour needed and thus, reduce your overall loading and unloading expenditures.
Automate Important Processes
Gone are the days when an entire warehouse could be run offline. In the current scenario, eCommerce companies rely heavily on the use of technology for important processes such as automatically assigning orders to a shipping company whenever they are placed, identifying which product needs to be selected and packaged through a WMS, and mentoring important data across warehouses and selling platforms through a single dashboard. These processes remove clutter and allow all your processes to be carried out smoothly. Additionally, you can purchase robots that further automate the picking, packaging and loading of goods.
Ensure That Vehicles are Consistently Maintained
The most important aspect of eCommerce transportation is the vehicles themselves and ensuring that they are running smoothly is extremely important. The last thing you or your customers would want is a random breakdown, adding multiple hours or days to the delivery timeline. By ensuring that the vehicle fleet of either your company or the shipping company you have partnered with is constantly maintained and checked for any issues that could cause a delay, you will save yourself a lot of time and money in the long run. Your customers will receive their orders on time and you will not have to waste time and money sorting out various issues that could happen during the delivery process.
Conclusion: What Services Does WareIQ Offer to Reduce Distribution Costs?
Finding ways to reduce transportation costs in their distribution network is of utmost importance to retailers that understand the implications if their expenses go beyond the budget. With just a little bit of effort and common sense, reducing distribution costs is very achievable for even the smallest retailers. It will help them provide better service, limit their expenditure and also leave more room to expand in the future. If you are an eCommerce retailer that is looking for ways to reduce transportation costs in your business, WareIQ can be the solution you need.
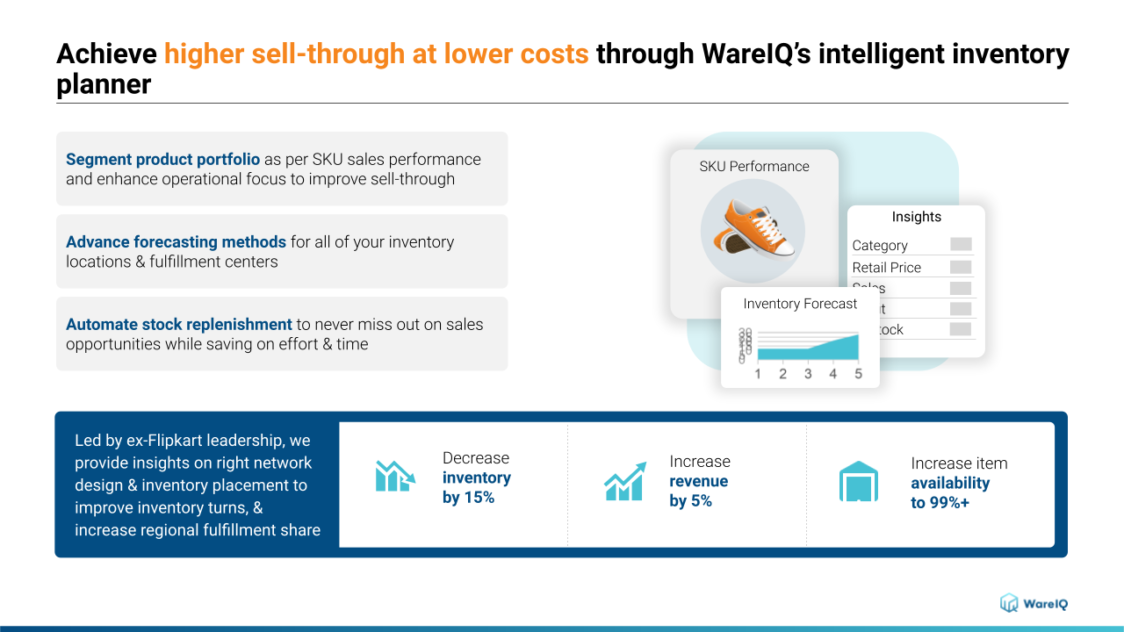
WareIQ is an eCommerce fulfillment company based in India and has emerged as one of the fastest-growing options in the country. We provide a wide range of eCommerce services that will help your business thrive. In relation to reducing your eCommerce transportation costs, we offer the following solutions:
Pan-India Network of Fulfillment Centers and Dark Stores
We provide a nationwide network of fulfillment centers and dark stores with smart inventory placement that will suggest the best storage location for each SKU based on its demand and target audience. This will enable you to store your goods closer to your customers and reduces the distance and time it takes to fulfill every order. We also offer dark stores for hyper-local delivery in specific locations.
Ultra-Fast Shipping
We have partnered with more than 20 of the biggest shipping aggregators in the country and will automatically assign the fastest and most cost-effective option for every order, resulting in quicker fulfillment and reduced shipping prices. If there is a delay on one route, we can instantly assign your order to another company.
Custom Packaging
We offer custom packaging facilities to help you reduce the overall footprint of your products, which will help it take up less space so that more units can be fulfilled at the same time. Your orders will also take up less space while being transported, which will reduce distribution costs even further.